Proven Steel Protection Projects Across Diverse Industries
Explore V&S Galvanizing's comprehensive portfolio of successful galvanizing case studies demonstrating superior steel protection across industrial construction, infrastructure, energy, and specialty applications. Our industrial galvanizing examples showcase proven performance, innovative solutions, and exceptional results that deliver long-term value for clients nationwide.
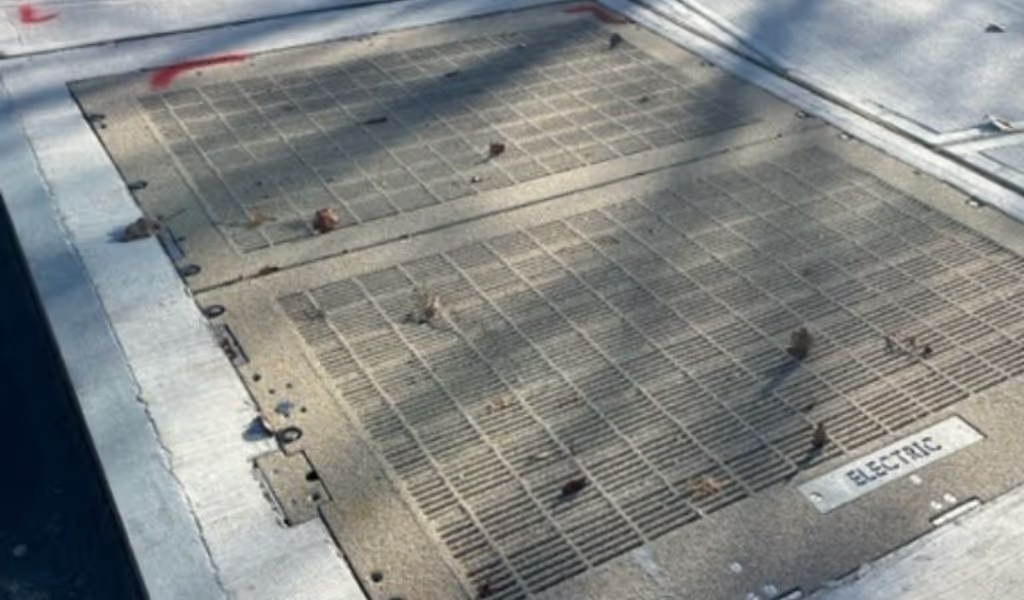
Access Hatch Solutions
Custom access hatches manufactured in Phoenix, NY feature hot-dip galvanized frames with epoxy aggregate coatings that provide 300 lb. per sq ft pedestrian-rated fall protection while seamlessly blending with sidewalk aesthetics.
.jpg)
Evolve: World Class Transporters
Hot-dip galvanizing transformed Evolve's custom transport trailers through an innovative three-section manufacturing approach that maximized cost-effectiveness while delivering superior durability and corrosion protection. This collaboration resulted in five galvanized transporters with long-lasting performance.
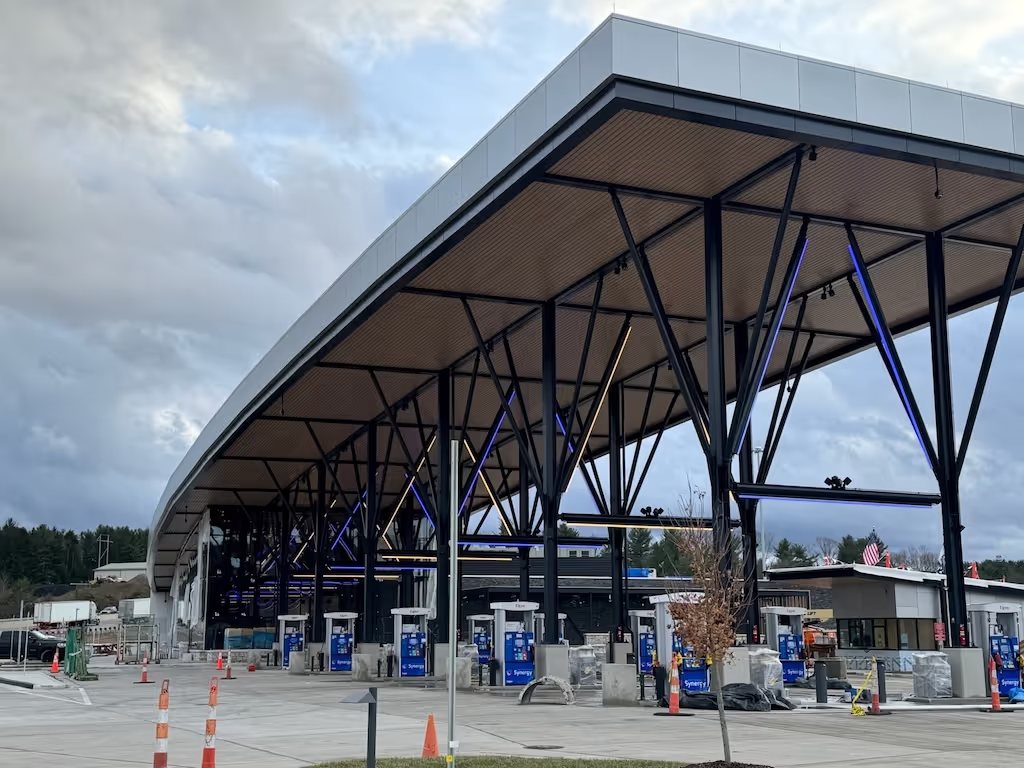
Bluestone Travel Plaza
West Virginia Steel's travel plaza project showcases seamless collaboration with expedited weekend galvanizing schedules to meet tight delivery timelines. The duplex coating system ensures these traveler amenities will provide durable service for years, with both travel plazas completed on schedule.
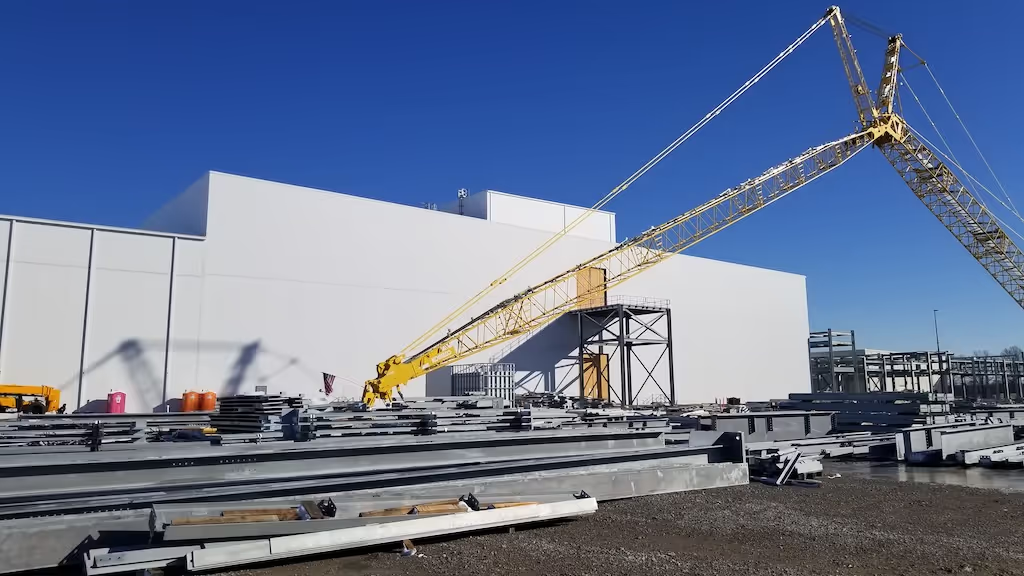
Purina Nestle Cooper Steel Green Acres
Nestlé Purina’s $550M pet food facility in Batavia, OH—its first new factory since 1975—will create 300 jobs and feature advanced robotics. Cooper Steel and the galvanizer partnered to deliver over 3,500 tons of steel across 150+ truckloads on a fast-track timeline, ensuring on-time delivery for this massive 1.2M sq ft project.
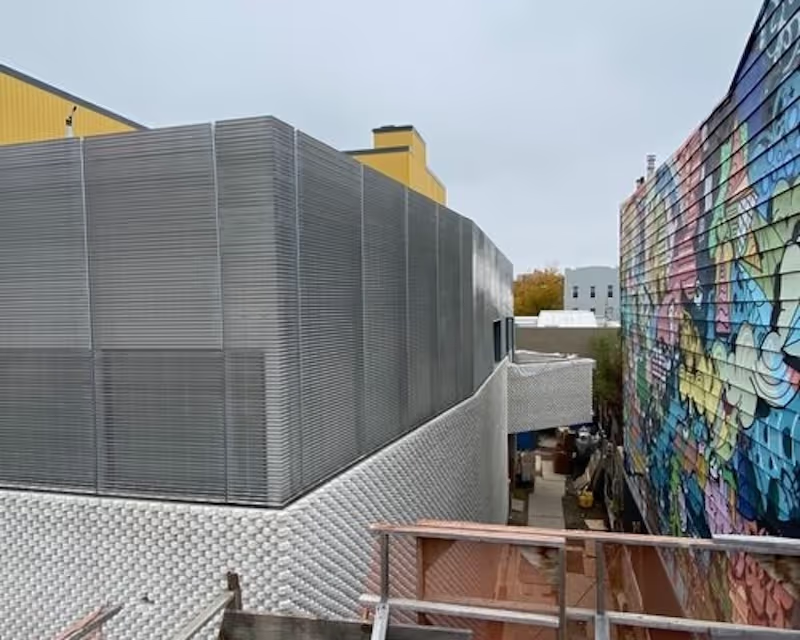
Maujer Street Facade
Hot-dip galvanized Orsogril panels delivered an industrial aesthetic for the Maujer Street building while providing fast installation, cost-effectiveness, and low maintenance requirements. The 3,260 square feet of galvanized panels create functional architectural artwork with coating durability designed to last decades.
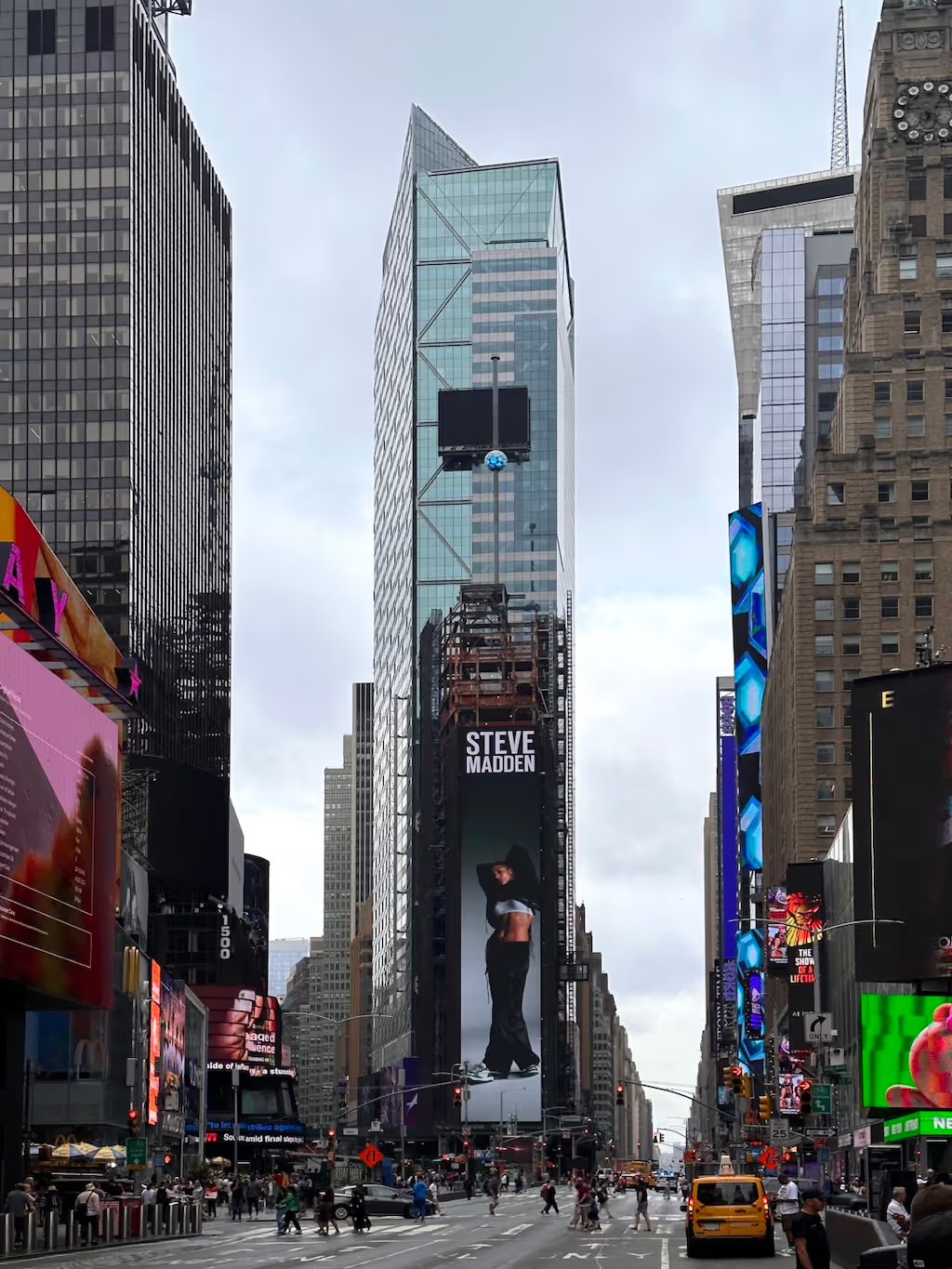
One Times Square
Hot-dip galvanizing enabled rapid construction for One Times Square's $500 million transformation, with 220 tons of steel processed in just two days to create the maintenance-free skeleton façade supporting the iconic ball drop building's new museum and viewing deck. This "set it and forget it" approach eliminated costly paint system maintenance while facilitating the historic landmark's evolution into a 12-floor visitor destination.
.avif)
Bridge Port I
BridgePort I's 243,600 square foot distribution center on a remediated 60-acre site required 25 tons of hot-dip galvanized steel for rooftop access systems, with proximity to the galvanizing facility enabling direct delivery of large sections for seamless installation.
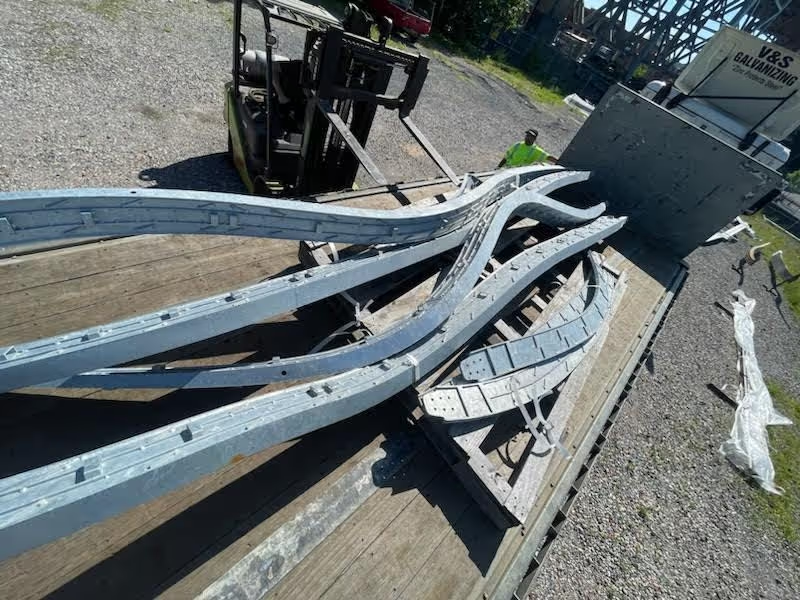
One uCity Square
This custom steel sculpture was engineered specifically for hot-dip galvanizing with careful consideration of kettle dimensions, drainage placement, and warping prevention, then finished with a striking 2-part epoxy coating in blue and brown. The project transformed rigid steel into fluid movement while achieving lasting durability through galvanized corrosion protection and vibrant color finishes.
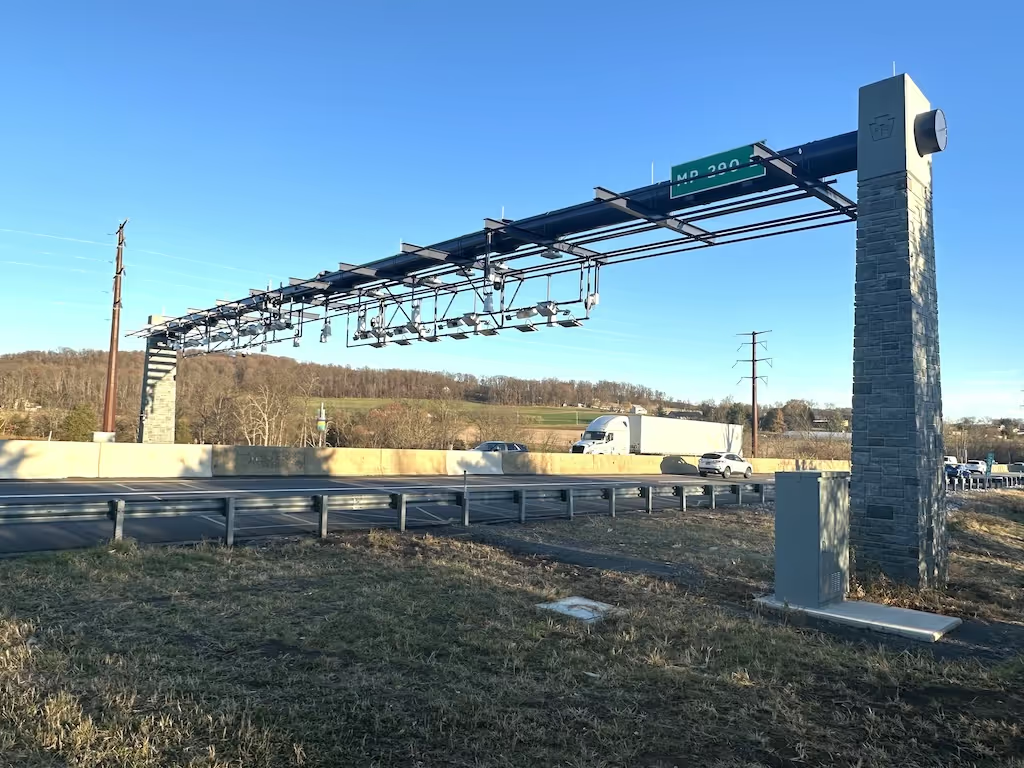
Pennsylvania Turnpike Road Tolling
Pennsylvania Turnpike's Open Road Tolling system features hot-dip galvanized gantries with duplex coating systems that support cashless, free-flowing toll collection estimated to save over $25 million annually. This corrosion-resistant infrastructure enables efficient traffic flow while reducing emissions and fuel consumption for the 86% of customers using PA EZ-Pass.
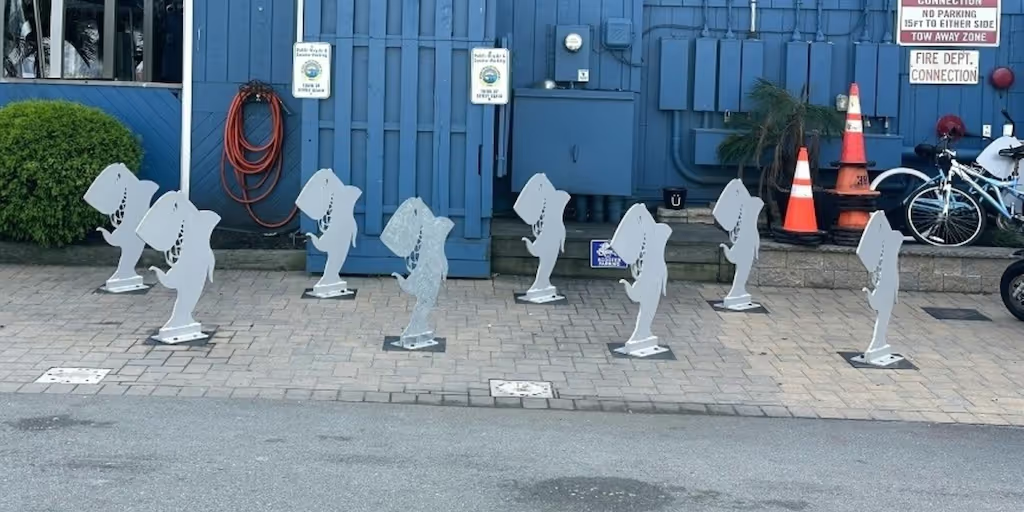
Starboard Bike Racks
The Starboard restaurant's iconic shark-shaped bike racks were restored through hot-dip galvanizing after coastal elements and heavy use degraded their original powder coating. This corrosion-resistant upgrade ensures the popular Dewey Beach landmark's distinctive bike storage will withstand Atlantic coastal conditions for years to come.
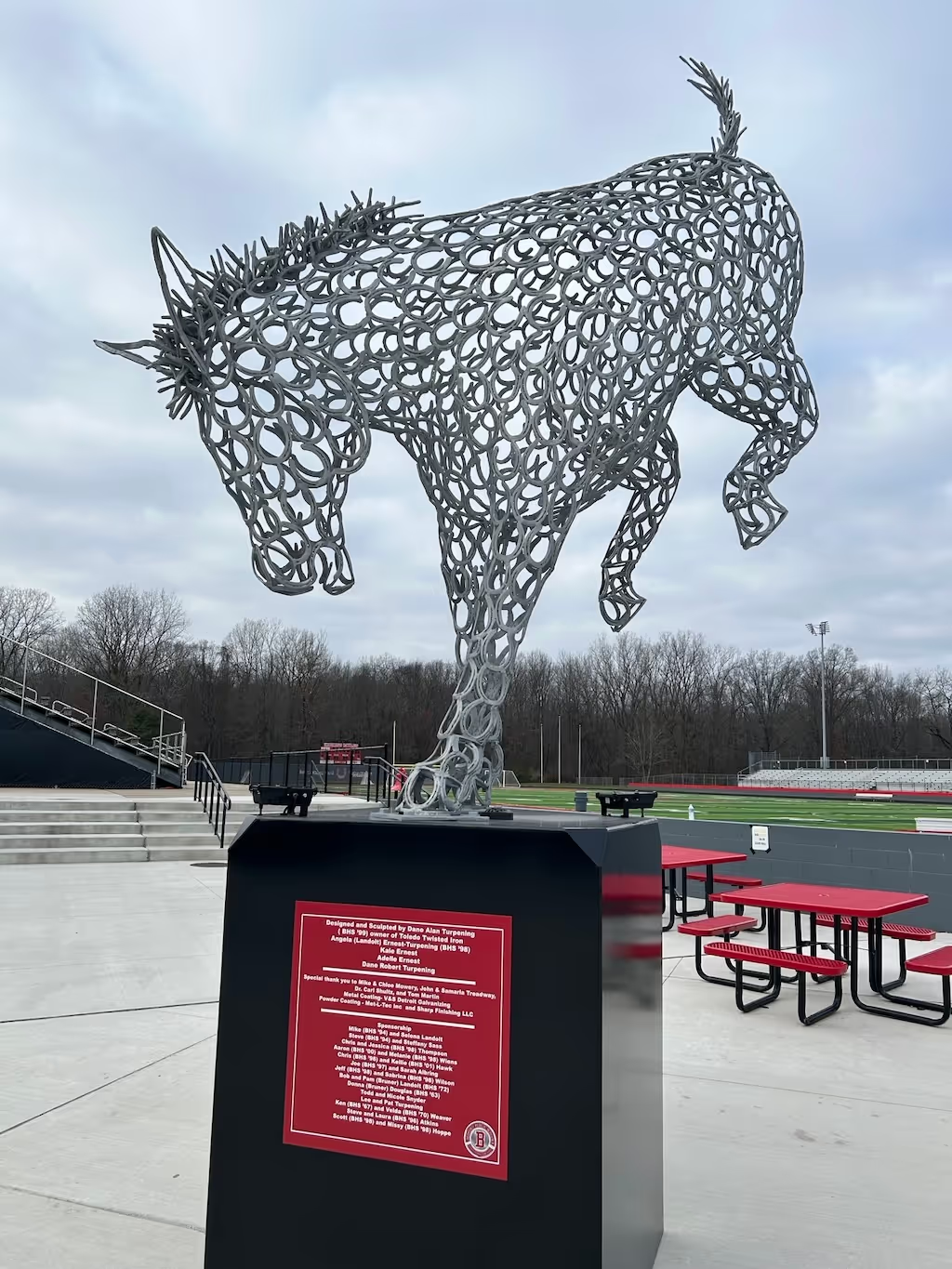
Bedford High School
Bedford High School's "Kicking Mule" mascot statue was crafted from over 750 recycled horseshoes donated by the local Amish community and hot-dip galvanized to ensure long-lasting durability at the football stadium entrance. This 715-pound community project was completed through donated materials and services for the 2024 homecoming celebration.
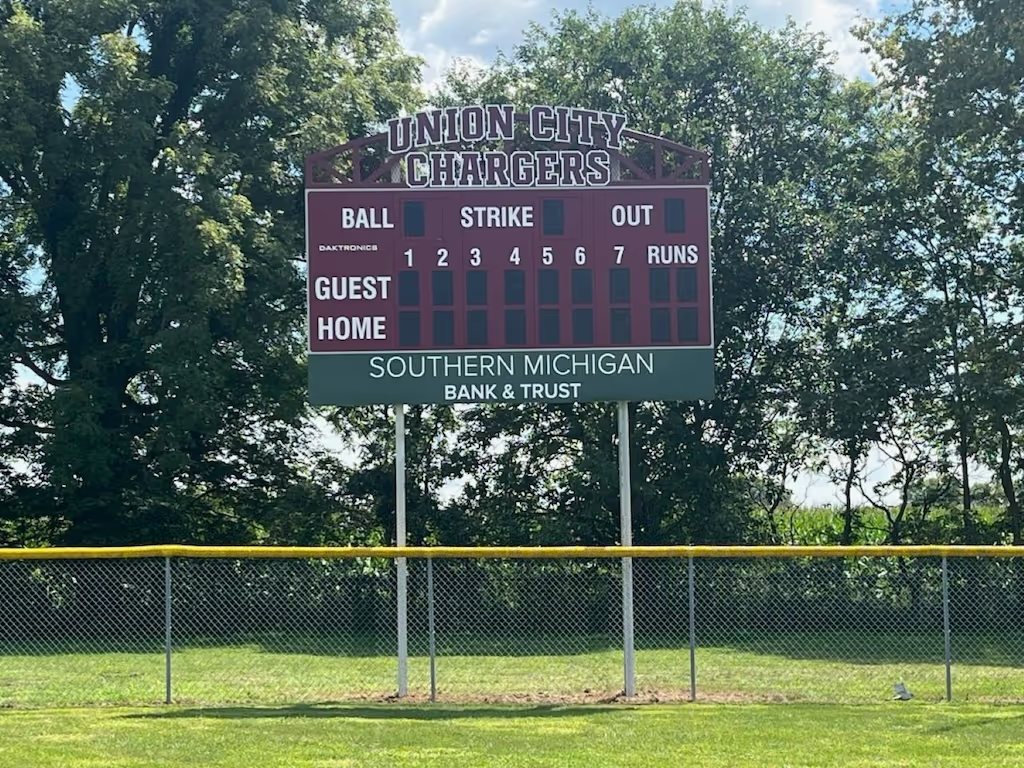
Union City Scoreboard
VS Detroit Galvanizing partnered with RA Fabricating to donate galvanizing services for new football and baseball scoreboards at Union City High School, creating durable 5,000-pound structures that will serve the community's athletic programs for years to come.
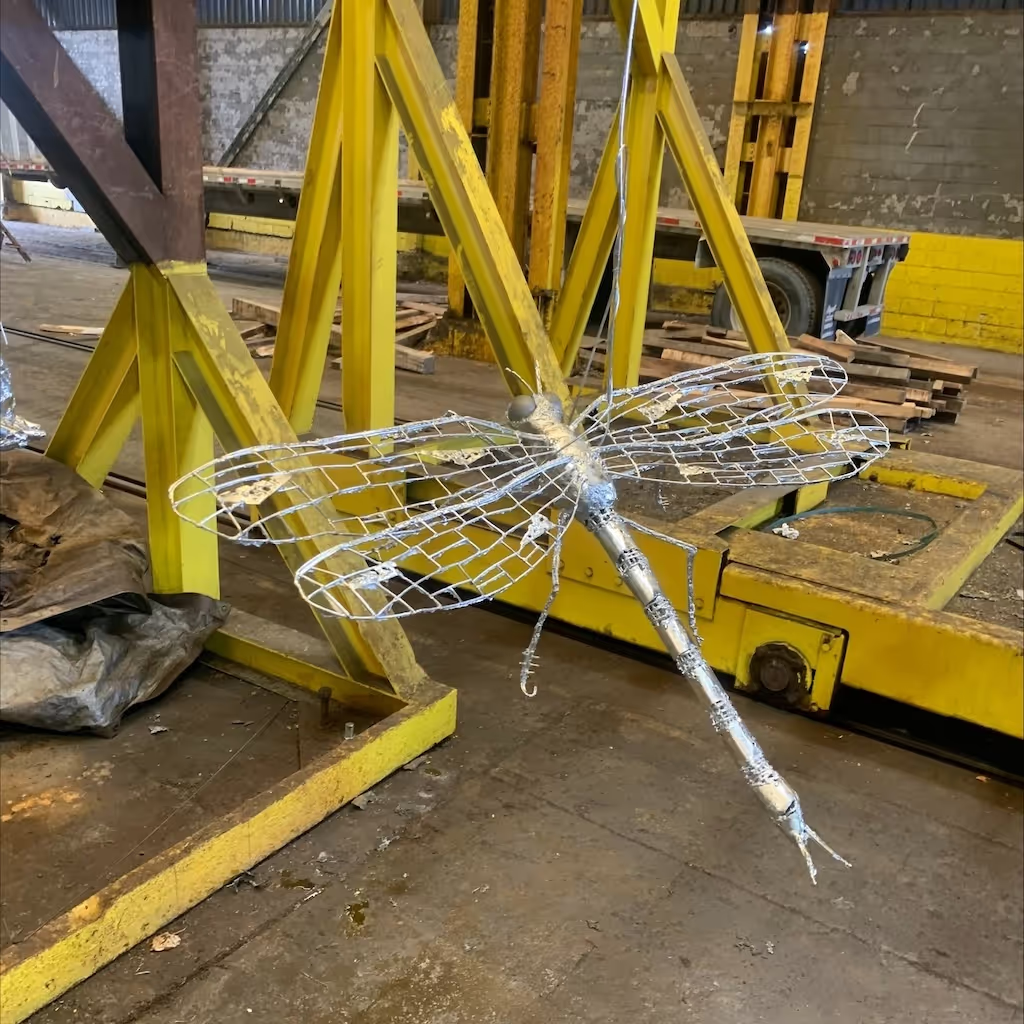
William Allen Art
Artist William Allen creates distinctive sculptures in his garage workshop, utilizing hot-dip galvanizing to achieve a sleek industrial aesthetic while ensuring long-lasting durability and visual appeal. His galvanized pieces offer contemporary metallic finishes that capture light beautifully, making fine art accessible to collectors and art enthusiasts alike.
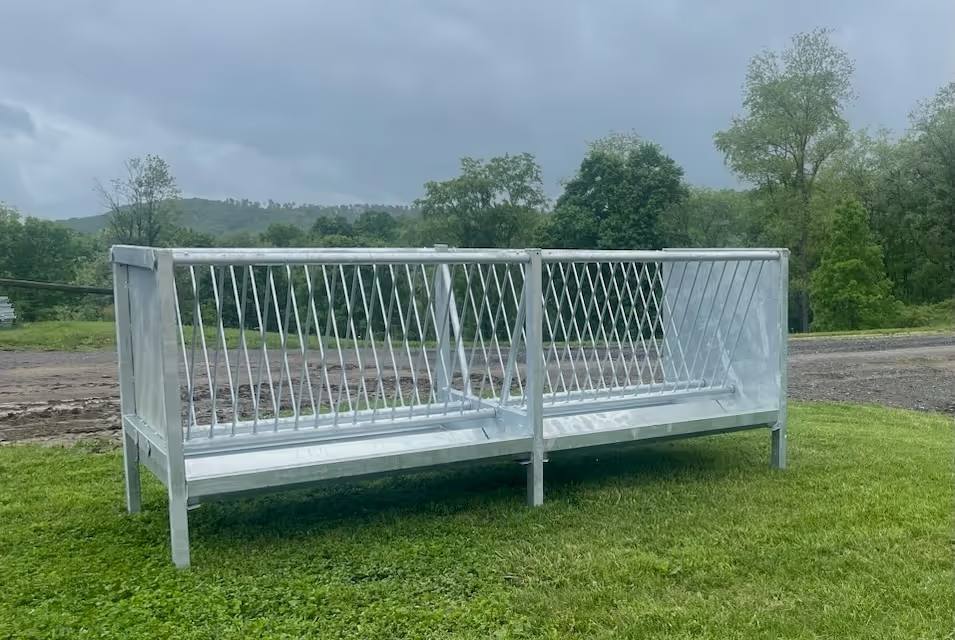
SQ Balefeeders
Modular large square bale feeders were developed for 3x3x8 bales, utilizing hot-dip galvanizing for ultimate corrosion protection in livestock operations serving up to 45 adult sheep or goats per feeder. The component-based design enables flat freight shipping and flexible on-site assembly into 10 or 15-foot configurations for various farm operations.

Knoebels Giant Log Flume
Knoebels Amusement Park's popular log flume ride underwent major refurbishment in 2023, with both new manufactured parts and existing components receiving hot-dip galvanizing to combat corrosion from 33 years of exposure to chlorinated water environments. The tight winter timeline ensured the beloved attraction would be ready for eager patrons when warm weather returned.
.avif)
Tait Ave Bridge
Tait Road Bridge's 85-foot replacement utilized hot-dip galvanized steel girders, guardrail, and decking to meet critical timeline requirements while providing long-term corrosion protection in the corrosive environment near Otter Creek. The county chose galvanized steel for its material availability, cost-effectiveness, and durability under urgent replacement conditions.
.avif)
Madison Bus BRT Shelter
Madison's bus rapid transit system Phase 1 features 45 stations with hot-dip galvanized and painted tube steel construction, requiring close fabricator-galvanizer coordination for proper vent and drain placement on architecturally exposed structural steel elements. The duplex coating system delivers both required corrosion protection and desired aesthetic color for the transit infrastructure.
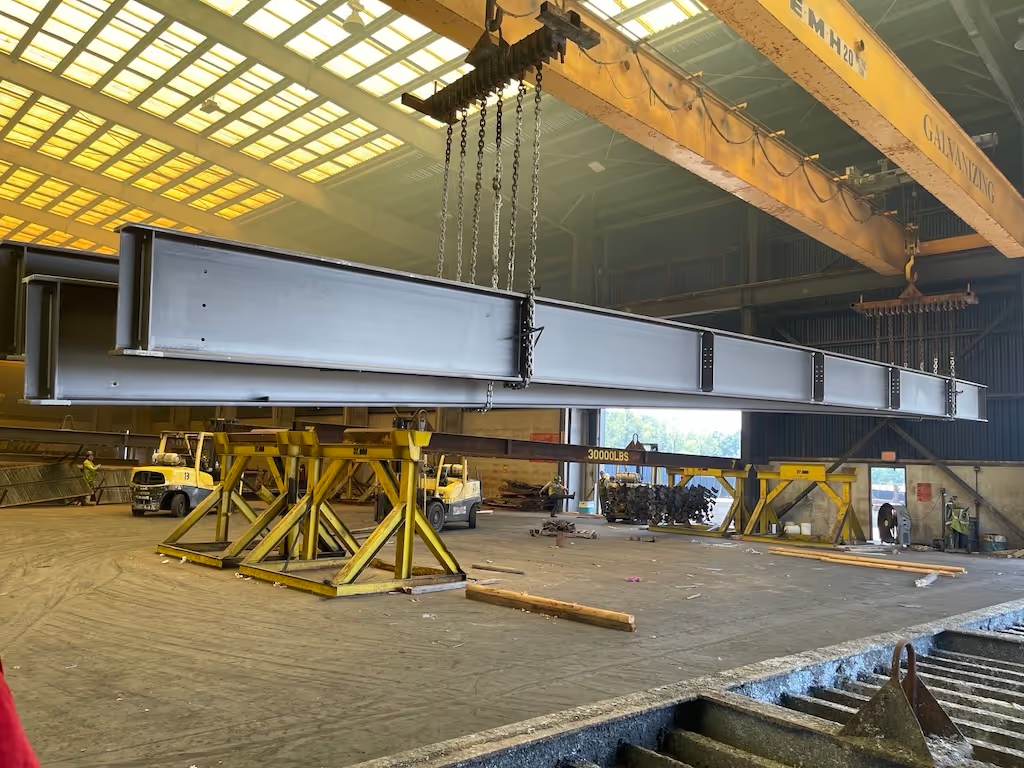
Pinecrest I74 Bridge
The Pinecrest I-74 Bridge replacement features a 214-foot, two-span structure with hot-dip galvanized composite plate girders supporting cast-in-place concrete decking, designed to eliminate low clearance safety issues from the original 1959 bridge. IDOT specified galvanizing for its proven longevity value in bridge infrastructure, with staged construction maintaining traffic flow during replacement.
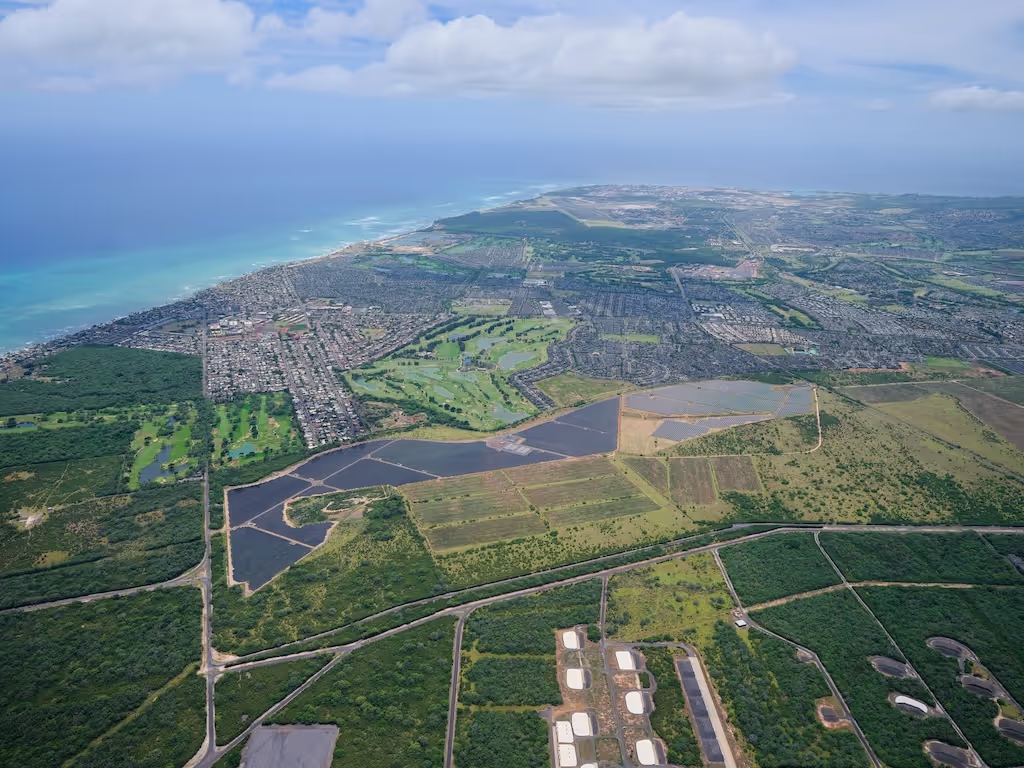
APA Hawaii Solar
The Ewa Beach Solar project in Kupono, Hawaii utilized 280 tons of hot-dip galvanized ground screws to support 120,000 solar panels, creating Oahu's largest renewable energy facility with four-hour battery storage capacity. Hot-dip galvanizing was selected for superior corrosion protection in the ocean-proximity environment, ensuring long-term durability for this major grid infrastructure project.
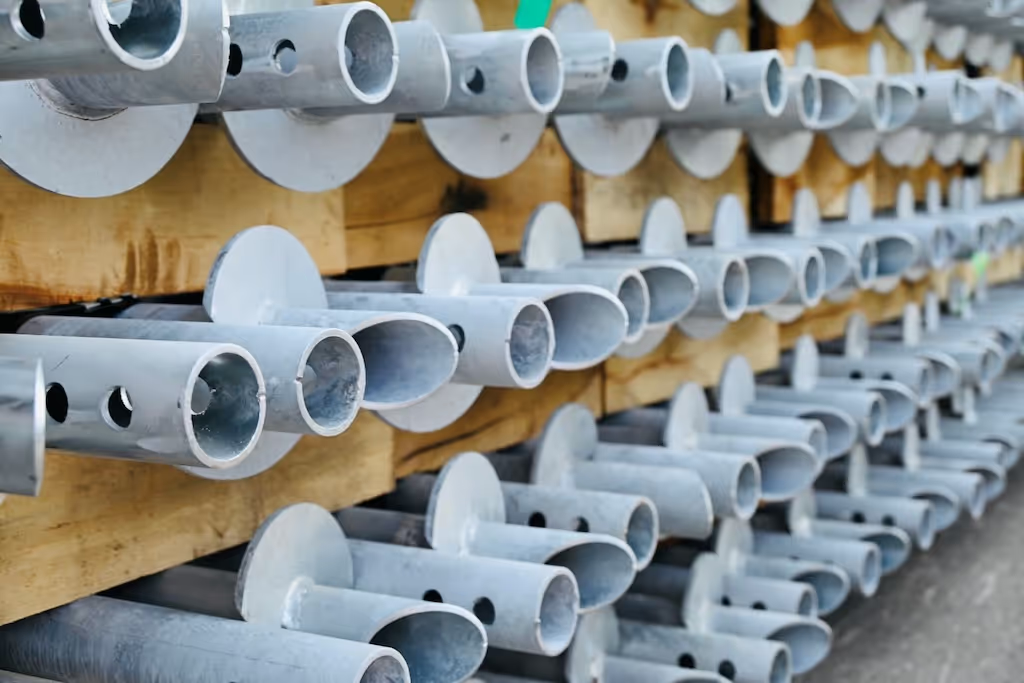
Finger Lakes Yacht Club
Yacht Club Cove Homeowners Association replaced aging wooden docks with a new aluminum dock system supported by 156 hot-dip galvanized helical piles installed by barge on Canandaigua Lake. The galvanized steel piles provide superior corrosion resistance in the marine environment, creating a durable foundation for the community's 84-home waterfront access system.
.avif)
Irish Hill Tower
The Irish Hill Tower in Upstate New York is an eight-story aircraft communication testing facility featuring hot-dip galvanized steel construction to withstand harsh winter conditions and provide durability for mounting aircraft equipment.
.avif)
Stonebridge Great Lakes
Great Lakes Cheese Co.'s $621 million facility required progressive hot-dip galvanizing of 1,400 tons of structural steel including box beams, tubes, and girts, with specialized hole plugging services for oversized tubular members.
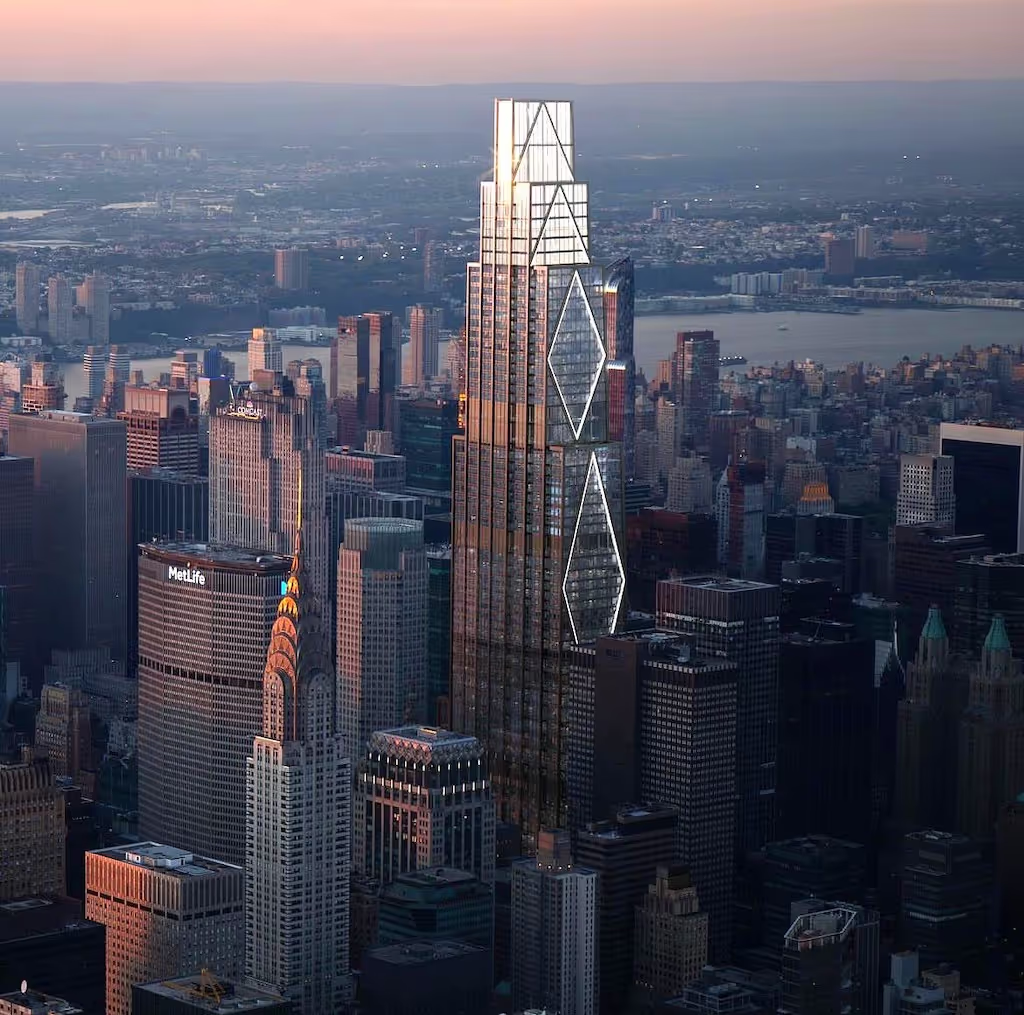
JPMorgan Chase 270 Park Ave
JPMorgan Chase's 60-story, 2.5 million square foot headquarters at 270 Park Avenue utilized 1,500 tons of hot-dip galvanized steel for upper floors to combat corrosive conditions from heat and moisture generated by electrical equipment. This $3 billion supertall structure is the tallest building in New York completely powered by hydroelectric energy.

Connesville Bridge
Crawford Avenue Bridge's $11.5 million rehabilitation project replaced the 65-year-old structure with a 490-foot, six-span steel stringer bridge featuring hot-dip galvanized girders, cross frames, and splice plates for corrosion protection near the Youghiogheny River. The new design includes expanded vehicle capacity, a seven-foot bike lane, and six-foot sidewalk for enhanced pedestrian and bicycle safety.
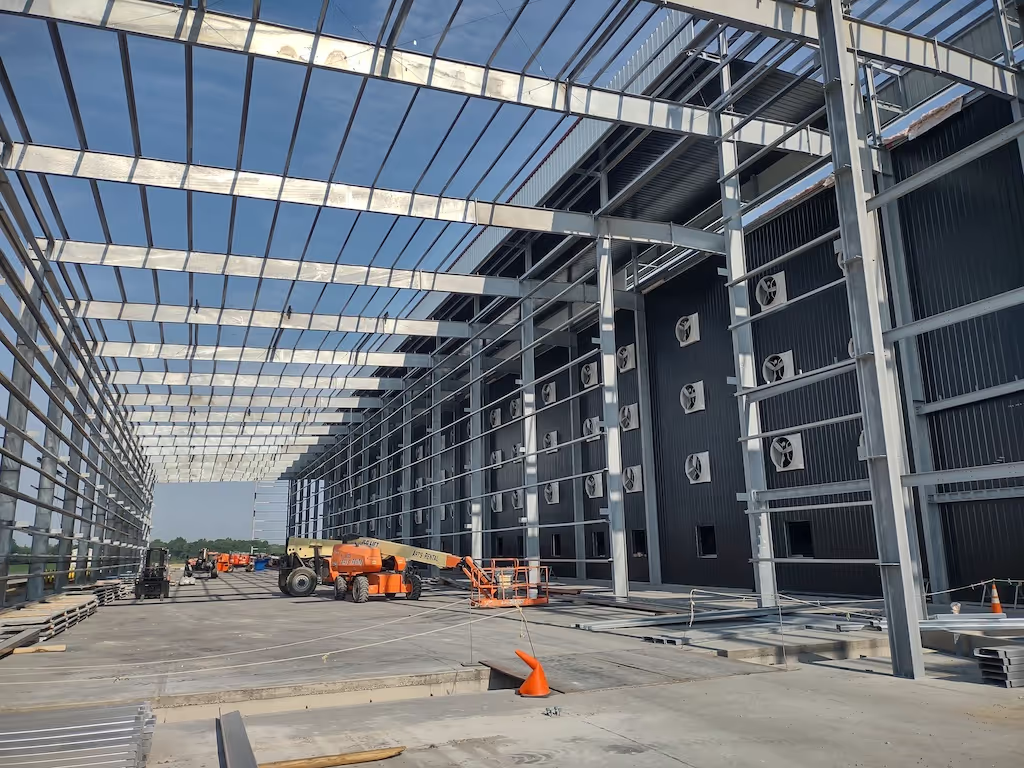
Golden Giant Egg Processing Facility
Golden Giant Building Systems' automated egg processing facility in western Ohio utilized 700,000 pounds of hot-dip galvanized steel to support operations producing 145,000 dozen eggs daily from over two million chickens.
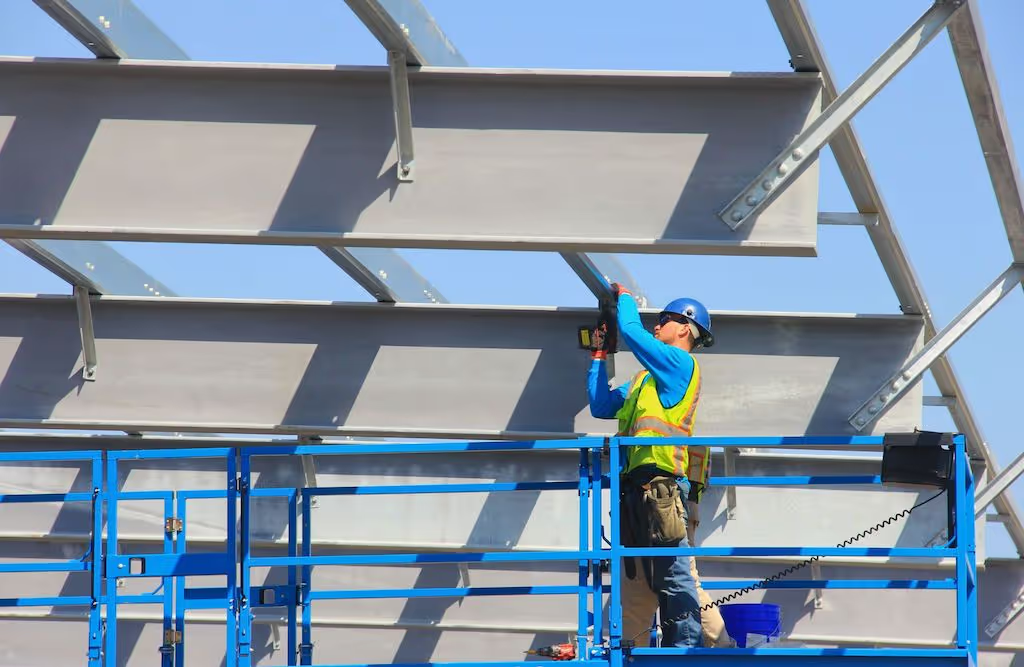
Farmingdale High School Carport
Farmingdale High School's 946.7KWDC solar carport system utilized 72 tons of hot-dip galvanized steel including anchor bolts, columns, tube arms, and purlins, with 24-hour turnaround schedules enabling seamless installation without blocking parking spaces.

Smithsonian National Zoo Lynx Exhibit
The Smithsonian National Zoo's new Canadian Lynx and Bat-eared Fox exhibit features hot-dip galvanized and painted round pipe columns with specialized lifting points to support protective netting in an intimate viewing environment. The duplex coating system provides durability against both weather elements and climbing animals that may scratch the paint over time.
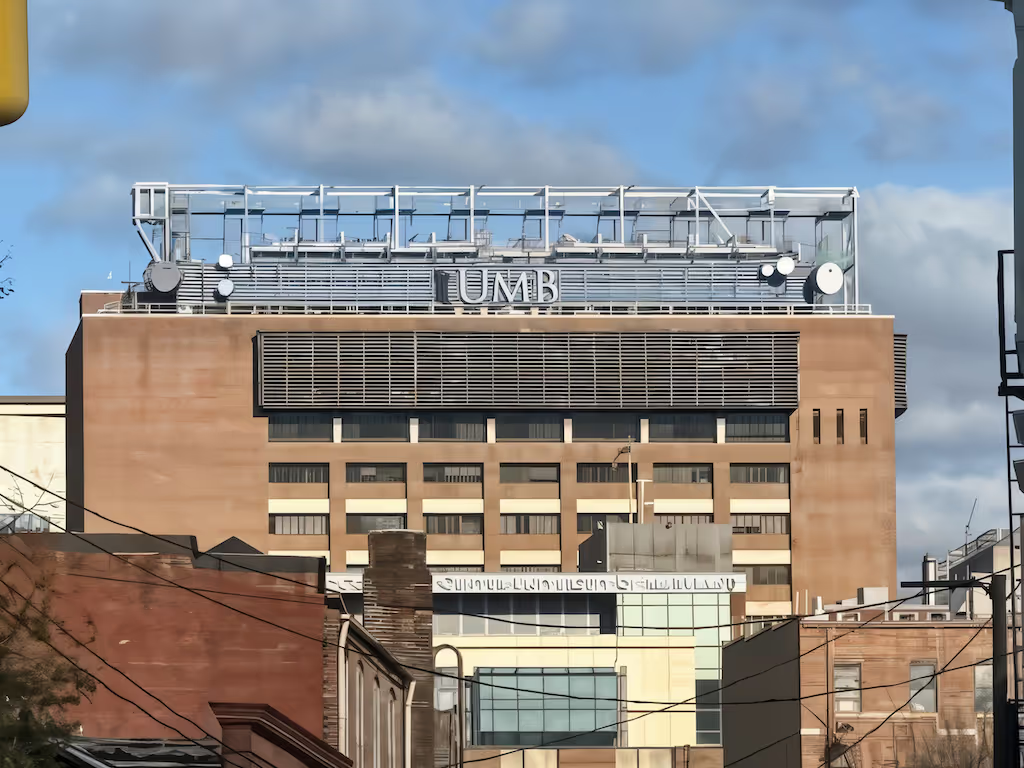
UMB Maintenance Bay
The University of Maryland School of Medicine's Bresler Research Center added a hot-dip galvanized rooftop maintenance bay with overhead crane system for servicing HVAC equipment on the 15-story building.
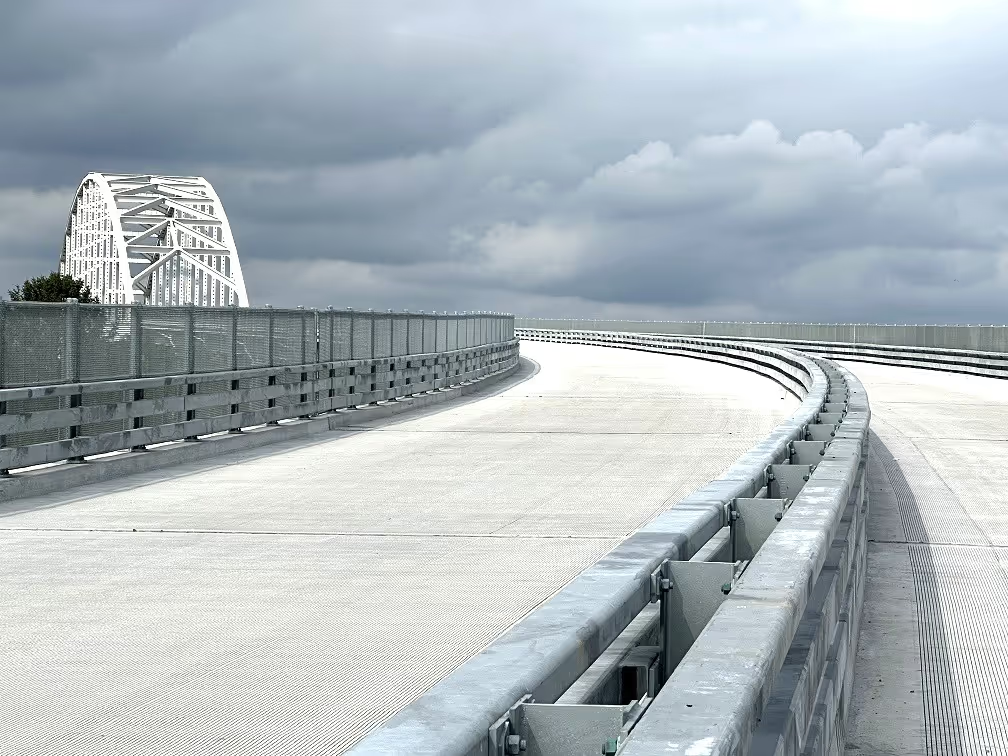
St. George’s Bridge
St. George's Bridge's 18-month renovation utilized hot-dip galvanized rails and barriers to replace corroded components, with the Army Corps of Engineers selecting galvanizing for longevity in harsh Mid-Atlantic coastal conditions along the C&D Canal.
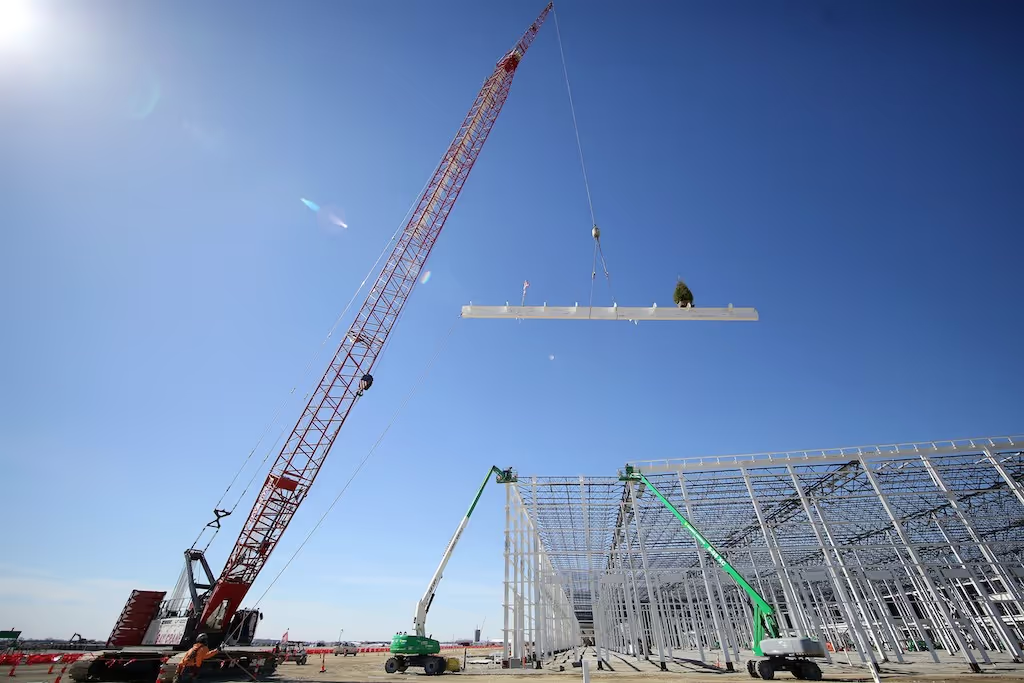
EV Battery Plant
LG Energy Solution and Honda's $4.4 billion joint venture EV battery plant in Jeffersonville, Ohio required over 1,000 tons of hot-dip galvanized steel across 2 million square feet, with 24-48 hour turnaround times to meet daily delivery schedules for this massive facility creating 2,200 jobs.
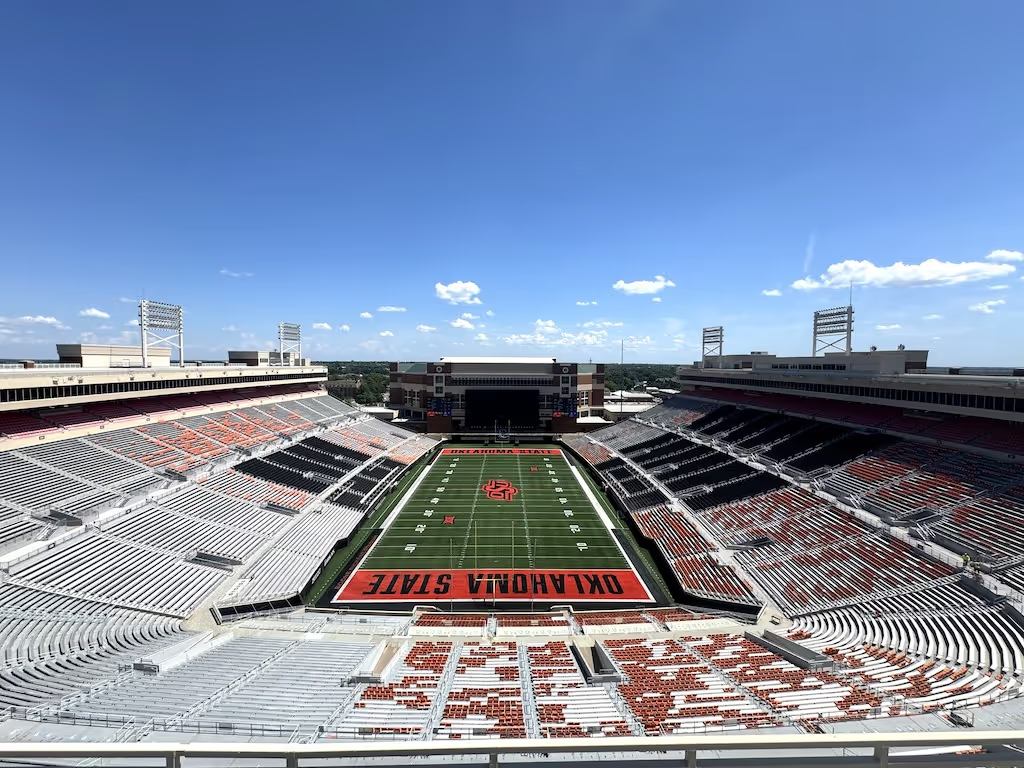
Oklahoma State Boone Pickens Stadium Renovation Phase 2
Oklahoma State University's $55 million Boone Pickens Stadium renovation utilized 1,800 linear feet of hot-dip galvanized handrails with specialized thread protection services and rapid 48-hour turnarounds to enhance fan safety and experience.

OSU Wexner Medical Center Inpatient Hospital
OSU Wexner Medical Center's $1.9 billion inpatient hospital tower utilized hot-dip galvanized steel for mechanical floors 7-10, including HVAC louvre support and curtain wall systems housing equipment at the top of Ohio State University's largest capital project in history.
Ready to Protect Your Projects Steel?
Partner with V&S Galvanizing to achieve superior results for your steel protection projects. Our proven track record across diverse industries demonstrates our capability to deliver exceptional galvanizing solutions that meet your specific requirements and exceed performance expectations.
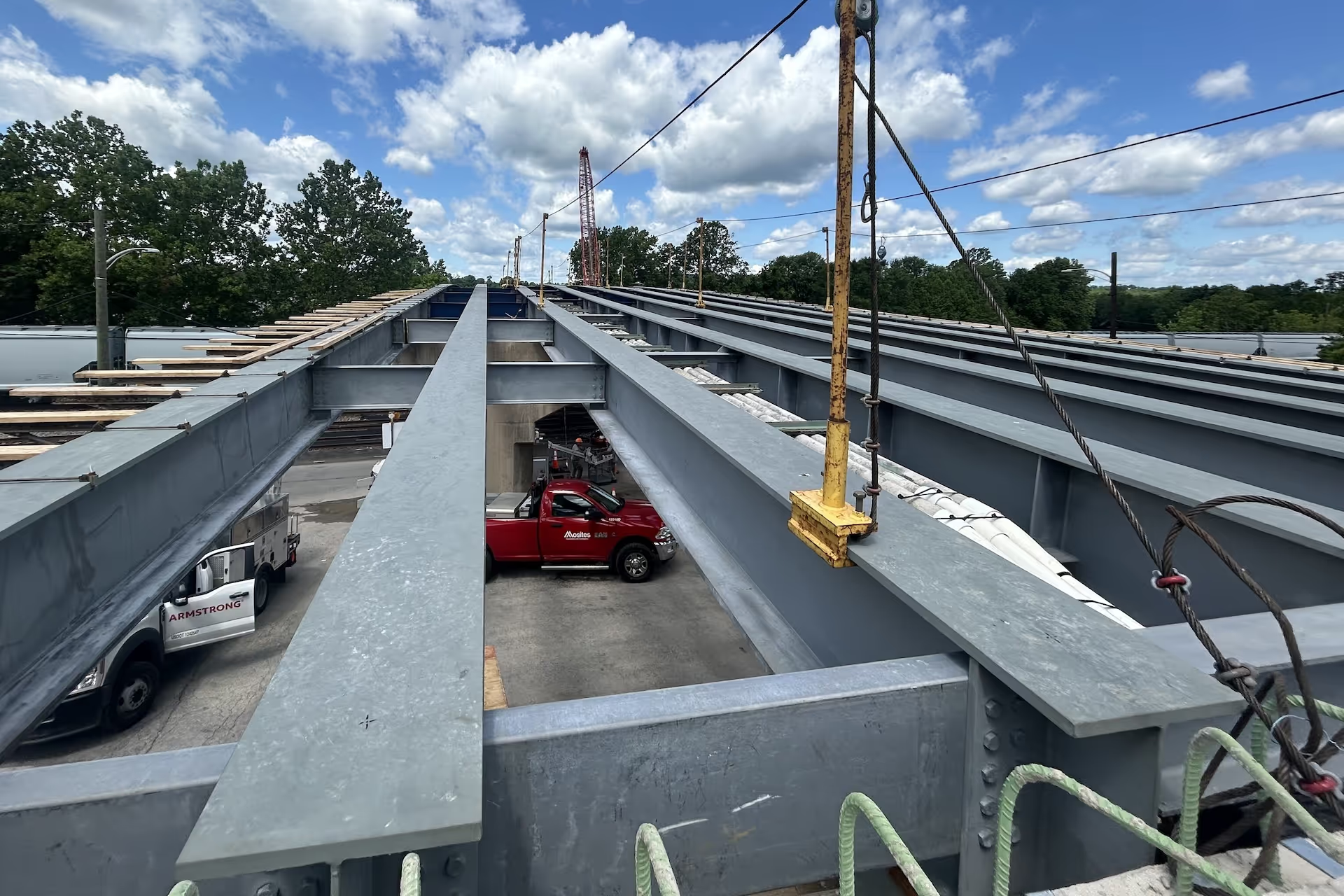