Precision Spin Galvanizing for Superior Fastener and Small Component Protection
V&S Galvanizing's spin galvanizing process delivers exceptional corrosion protection for fasteners, bolts, nuts, and small fabricated components through advanced centrifuge galvanizing technology. Our precision process ensures complete zinc coating coverage, optimal thickness, and superior finish quality for critical hardware applications requiring long-term reliability.
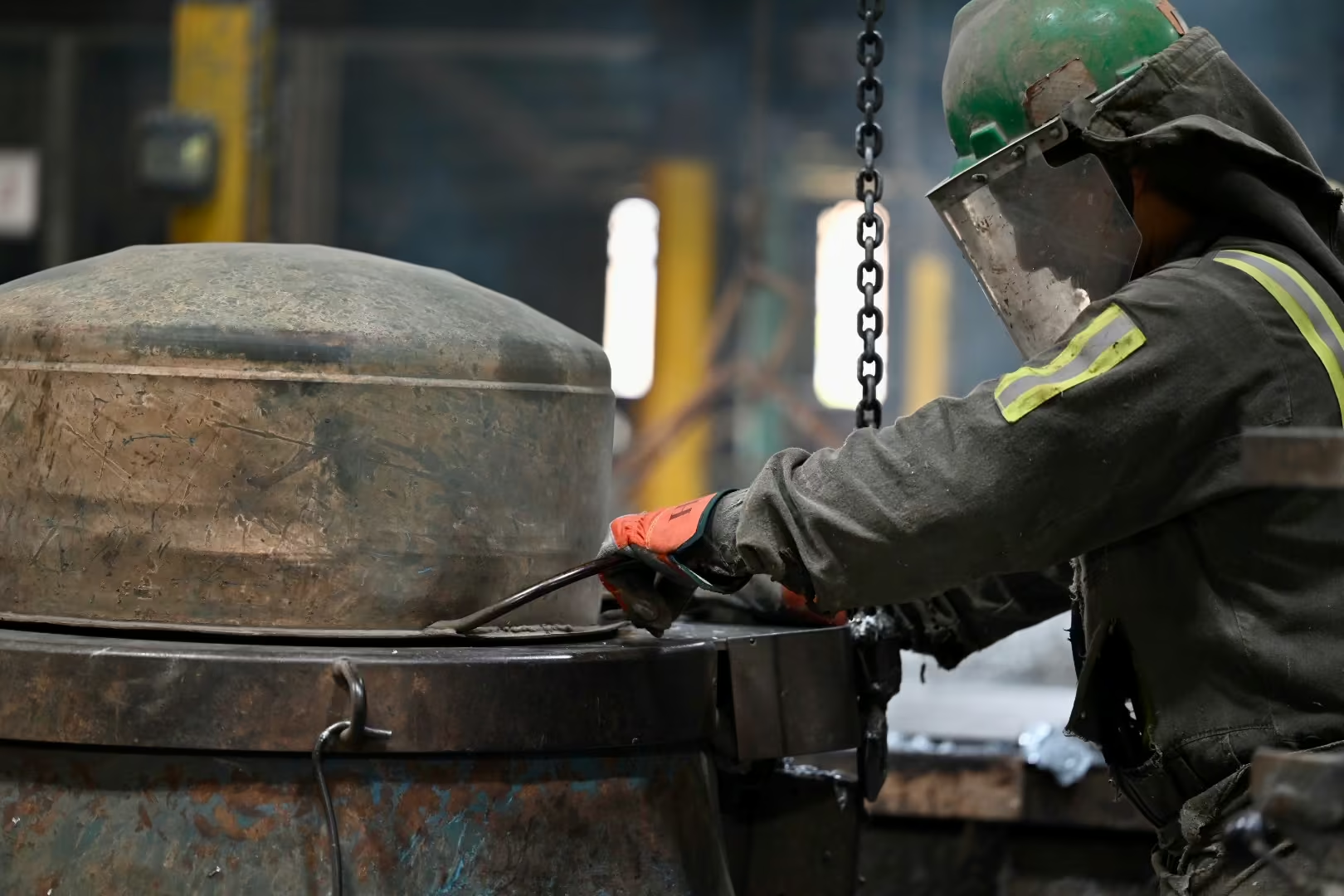
Our Advanced 10-Step Spin Galvanizing Process Delivers Precision Results
Our comprehensive spin galvanizing process combines traditional hot-dip galvanizing with centrifuge technology to achieve superior coating uniformity and finish quality. Each step is precisely controlled to ensure optimal coating thickness, complete coverage, and exceptional surface finish for fasteners and small components.
Component Inspection & Sorting
Detailed evaluation and categorization of fasteners and small components to ensure proper processing parameters and identify threading requirements.
Degreasing & Cleaning
Advanced alkaline cleaning removes manufacturing oils, lubricants, and contaminants to prepare component surfaces for optimal zinc adhesion.
Water Rinse
Thorough rinsing removes cleaning residues and prepares components for acid treatment while maintaining stringent quality control standards.
Pickling Treatment
Controlled pickling treatment removes scale, rust, and oxidation to create clean, uniform surfaces essential for superior zinc bonding.
Secondary Rinse
Complete removal of pickling residues ensures pristine surface preparation and prevents contamination of subsequent galvanizing steps.
Flux Application
Zinc ammonium chloride flux application prevents oxidation and promotes uniform zinc coating during the hot-dip immersion process.
Hot-Dip Galvanizing
Components are immersed in molten zinc at 840°F, creating metallurgically bonded zinc-iron alloy layers for maximum corrosion protection.
Centrifuge Spinning
High-speed centrifuge process removes excess zinc and ensures optimal coating thickness while maintaining thread integrity and dimensional accuracy.
Quenching & Cooling
Controlled cooling process prevents thermal stress while maintaining coating integrity.
Final Inspection & testing
Comprehensive quality control including coating thickness measurement, thread gauging, and visual inspection to ensure specification compliance.
Component Inspection & Sorting
Detailed evaluation and categorization of fasteners and small components to ensure proper processing parameters and identify threading requirements.
Degreasing & Cleaning
Advanced alkaline cleaning removes manufacturing oils, lubricants, and contaminants to prepare component surfaces for optimal zinc adhesion.
Water Rinse
Thorough rinsing removes cleaning residues and prepares components for acid treatment while maintaining stringent quality control standards.
Pickling Treatment
Controlled pickling treatment removes scale, rust, and oxidation to create clean, uniform surfaces essential for superior zinc bonding.
Secondary Rinse
Complete removal of pickling residues ensures pristine surface preparation and prevents contamination of subsequent galvanizing steps.
Flux Application
Zinc ammonium chloride flux application prevents oxidation and promotes uniform zinc coating during the hot-dip immersion process.
Hot-Dip Galvanizing
Components are immersed in molten zinc at 840°F, creating metallurgically bonded zinc-iron alloy layers for maximum corrosion protection.
Centrifuge Spinning
High-speed centrifuge process removes excess zinc and ensures optimal coating thickness while maintaining thread integrity and dimensional accuracy.
Quenching & Cooling
Controlled cooling process prevents thermal stress while maintaining coating integrity.
Final Inspection & testing
Comprehensive quality control including coating thickness measurement, thread gauging, and visual inspection to ensure specification compliance.
Component Inspection & Sorting
Detailed evaluation and categorization of fasteners and small components to ensure proper processing parameters and identify threading requirements.
Degreasing & Cleaning
Advanced alkaline cleaning removes manufacturing oils, lubricants, and contaminants to prepare component surfaces for optimal zinc adhesion.
Water Rinse
Thorough rinsing removes cleaning residues and prepares components for acid treatment while maintaining stringent quality control standards.
Pickling Treatment
Controlled pickling treatment removes scale, rust, and oxidation to create clean, uniform surfaces essential for superior zinc bonding.
Secondary Rinse
Complete removal of pickling residues ensures pristine surface preparation and prevents contamination of subsequent galvanizing steps.
Flux Application
Zinc ammonium chloride flux application prevents oxidation and promotes uniform zinc coating during the hot-dip immersion process.
Hot-Dip Galvanizing
Components are immersed in molten zinc at 840°F, creating metallurgically bonded zinc-iron alloy layers for maximum corrosion protection.
Centrifuge Spinning
High-speed centrifuge process removes excess zinc and ensures optimal coating thickness while maintaining thread integrity and dimensional accuracy.
Quenching & Cooling
Controlled cooling process prevents thermal stress while maintaining coating integrity.
Final Inspection & testing
Comprehensive quality control including coating thickness measurement, thread gauging, and visual inspection to ensure specification compliance.
Specialized Spin Galvanizing Capabilities for Precision Components
V&S Galvanizing's spin galvanizing facilities are equipped with state-of-the-art centrifuge systems capable of processing fasteners and small components with exceptional precision and consistency. Our specialized equipment handles components ranging from small bolts to large anchor bolts, ensuring optimal coating distribution and finish quality for every application.
Each spin galvanizing facility features multiple centrifuge units with variable speed controls, allowing precise optimization for different component types and specifications. Our automated material handling systems ensure efficient processing while maintaining strict quality control throughout the galvanizing cycle.
Advanced process monitoring systems track centrifuge speeds, zinc temperatures, and coating thickness in real-time, ensuring consistent results across all production runs. Our integrated quality assurance protocols guarantee that every component meets or exceeds industry standards for coating performance and dimensional accuracy.
Spin Galvanizing for Critical Fastener Applications
Superior Thread Preservation
Maintains Thread Integrity Centrifuge process removes excess zinc while preserving thread dimensions and functionality, eliminating the need for post-galvanizing thread cutting or rework.
Uniform Coating Distribution
Complete Coverage Assurance Spinning action ensures even zinc distribution and eliminates thick deposits or bare spots common with other galvanizing methods for small components.
Enhanced Finish Quality
Smooth, Professional Appearance Centrifuge process produces smooth, uniform surface finish that enhances both aesthetic appeal and functional performance of galvanized fasteners.
Optimal Coating Thickness
Precise Thickness Control Advanced spinning technology achieves optimal coating thickness for maximum corrosion protection while maintaining dimensional tolerances and fit requirements.
Fast Production Turnaround
Efficient Batch Processing Specialized equipment and streamlined processes enable rapid turnaround times for large fastener quantities while maintaining consistent quality standards.
Cost-Effective Protection
Maximum Value Investment Spin galvanizing provides superior corrosion protection at competitive costs, eliminating the need for expensive specialty fasteners or frequent replacements.
Spin Galvanizing FAQ
Find answers about our centrifugal galvanizing process for small parts, batch sizes, threading protection, and finishing quality.
Spin galvanizing provides superior finish quality, better dimensional control, and preserved thread integrity for small components.
Yes, we can process mixed fastener batches efficiently. Our experienced team sorts and processes components based on size, material, and coating requirements to ensure optimal results for all items in each batch.
Spin galvanizing provides controlled, uniform coating thickness that meets ASTM A153 standards, optimized for fastener applications. The centrifuge process ensures consistent coverage without thick deposits that could interfere with component function.
Our spin galvanizing equipment can handle components up to 36 inches in length with thread sizes from #10 through 4 inches in diameter, with batch capacities up to 2,000 pounds per processing cycle.
The centrifuge process removes excess zinc from threads while maintaining optimal coating thickness on all surfaces. This minimizes rather than eliminates the need for post-galvanizing thread cutting or rework, preserving original thread dimensions and functionality.
Spin galvanizing is ideal for fasteners, bolts, nuts, washers, small brackets, and hardware components typically under 36 inches in length. The centrifuge process ensures optimal coating distribution and thread preservation.
Yes, our spin galvanizing process uses centrifuge technology to achieve optimal coating thickness and finish quality for fasteners, bolts, nuts, and other small components while maintaining thread integrity.
Technical Resources for Spin Galvanizing Specifications
Access detailed technical documentation, coating specifications, and design guidelines specifically for spin galvanized fasteners and small components. Our engineering team provides expert consultation to ensure optimal performance and compliance with your project requirements.
Calculator
Estimate project turnaround and zinc usage with this galvanizing calculator. Plan smarter with quick, accurate insights tailored to your specifications.
Docs
Download detailed technical specifications, material guidelines, and coating standards to support your engineering and fabrication needs.
News
Stay informed with industry updates, company news, and best practices for corrosion protection and steel performance.
FAQs
Get answers to common questions about our galvanizing services, coating performance, project prep, and more—straight from the experts.