Golden Giant Egg Processing Facility
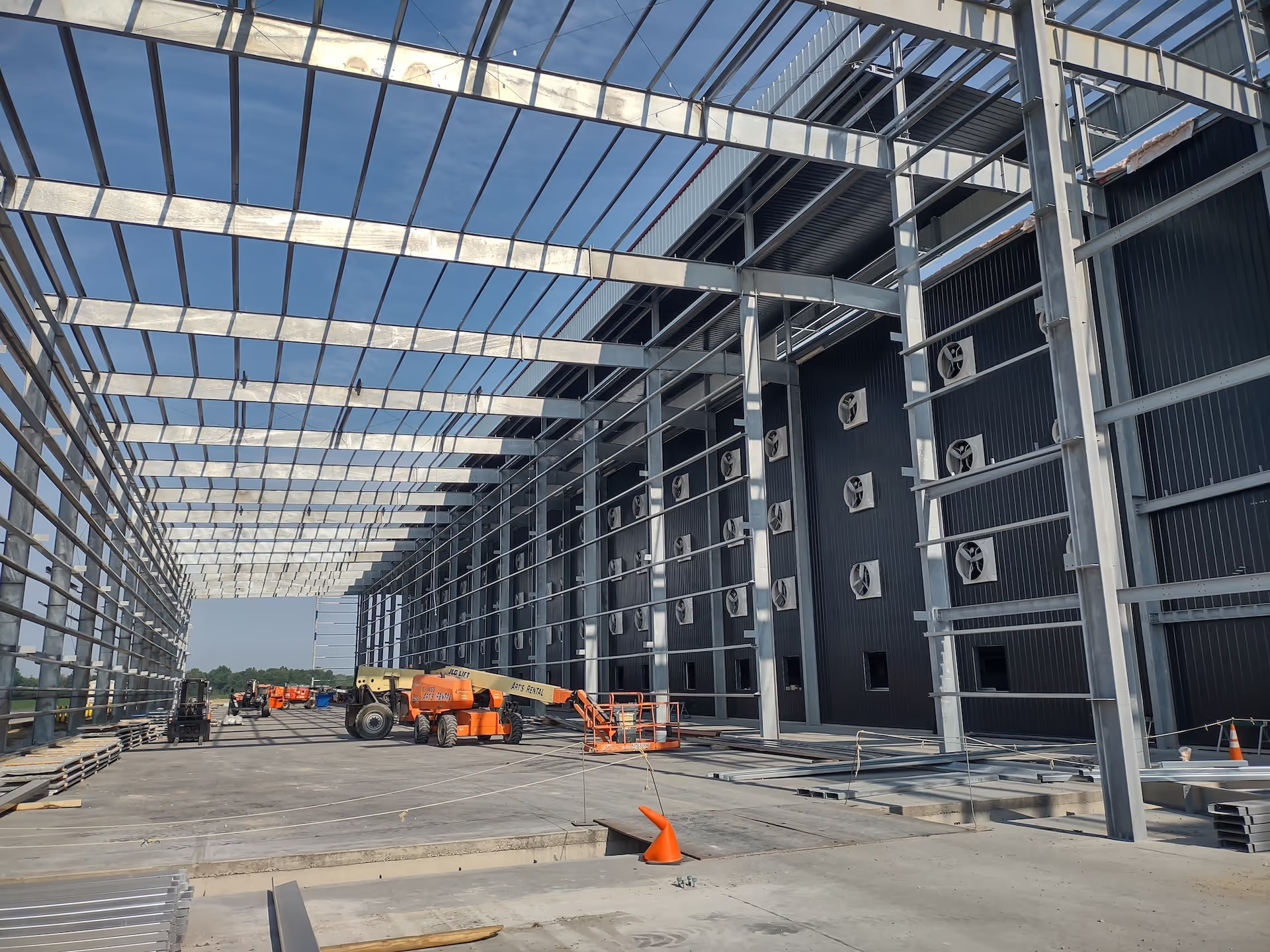
The Challenge, The Solution, The Results
Golden Giant Building Systems and the Egg Processing Company designed a state-of-the-art egg processing facility in western Ohio. The egg processing company, one of the largest privately owned and operated egg processing facilities in the Midwest, houses over two million chickens on the farm. They produce approximately 145,000 dozen eggs per day, that totals over 37 million eggs per year. It’s a fully automated facility from start to finish, quite a site to behold. The automated equipment washes and sanitizes the eggs and then stored at the processing plant. The egg is then transported to either the shell egg market or the egg products market. Each stage of this module, time and temperature variables are key. The ventilation system makes the difference, optimal climate temperature and relative humidity levels in the barn ensures a comfortable and consistent living environment for the laying hens, better egg production, and good animal health.
As mentioned earlier a 700,000 lb. project that took approximately 18 months to galvanize and install. The galvanizer worked closely with Golden Giant Building Systems to meet their scheduling demands. Inside sales / Plant Manager and Operations Manager effectively navigated the galvanizing of material for on-time deliveries. The constant communication made this project a success, based on the project results between galvanizer and Golden Giant, the next 400,000 lb. phase is coming to the galvanizer in December of 2024.
“It’s all about the eggs”
Protecting America's Infrastructure One Dip at a Time
.avif)
Stonebridge Great Lakes
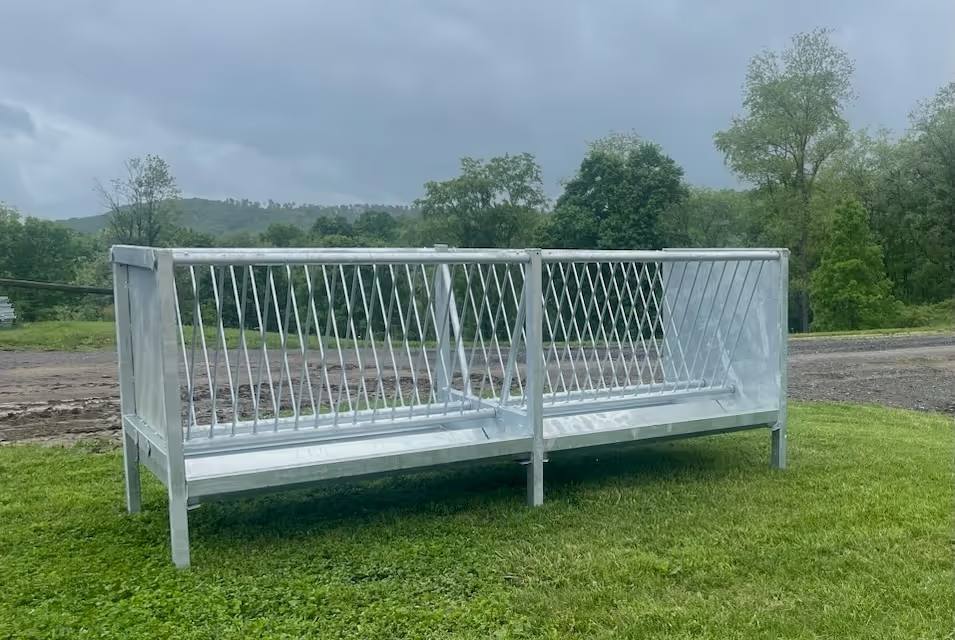
SQ Balefeeders
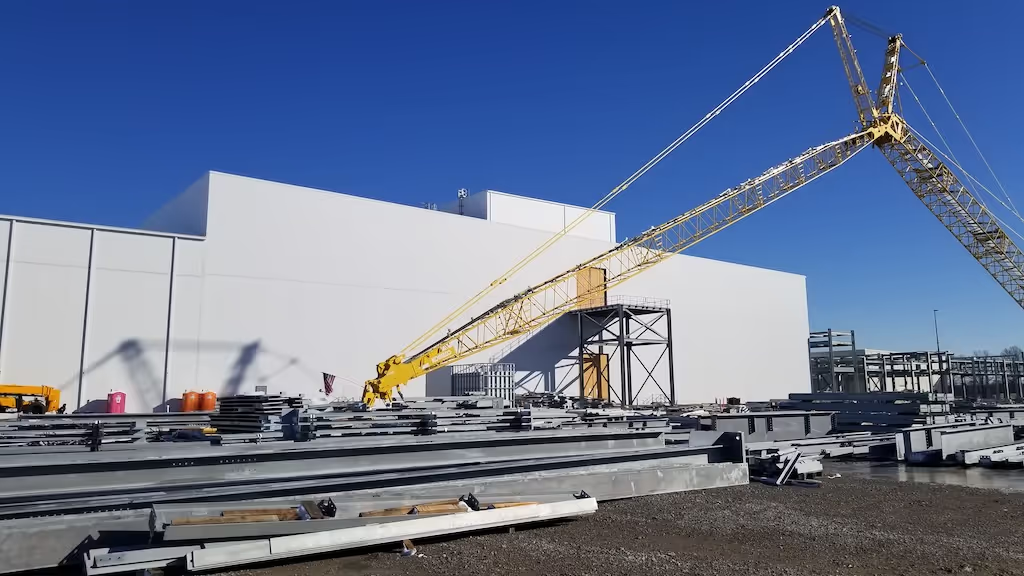
Purina Nestle Cooper Steel Green Acres
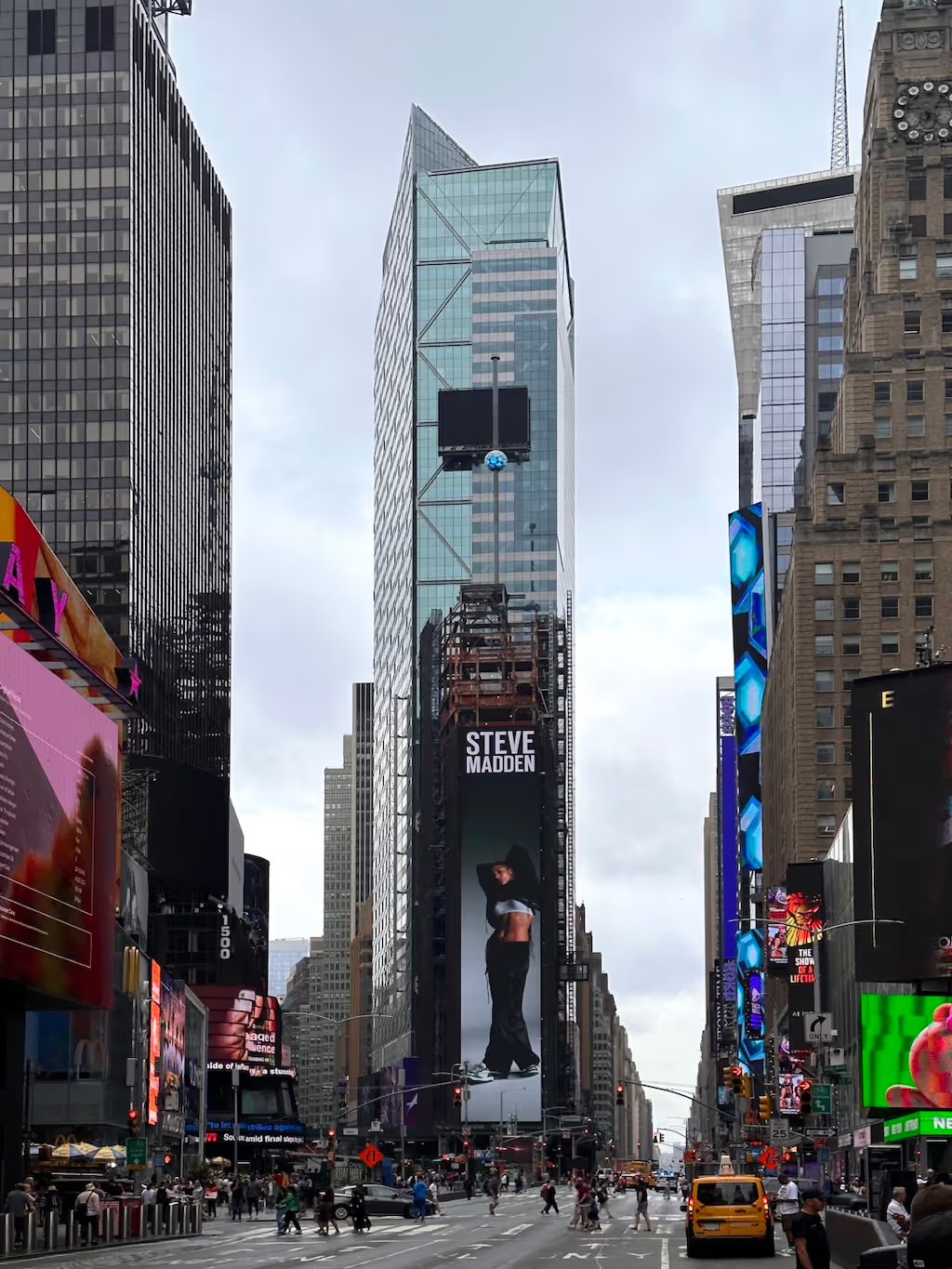
One Times Square
Ready to Transform Your Project with Industry-Leading Galvanizing?
Don't let corrosion compromise your investment. Partner with V&S Galvanizing for proven protection that outlasts the competition. Our expert team delivers custom solutions, rapid turnaround, and nationwide reliability that keeps your project on schedule and on budget.
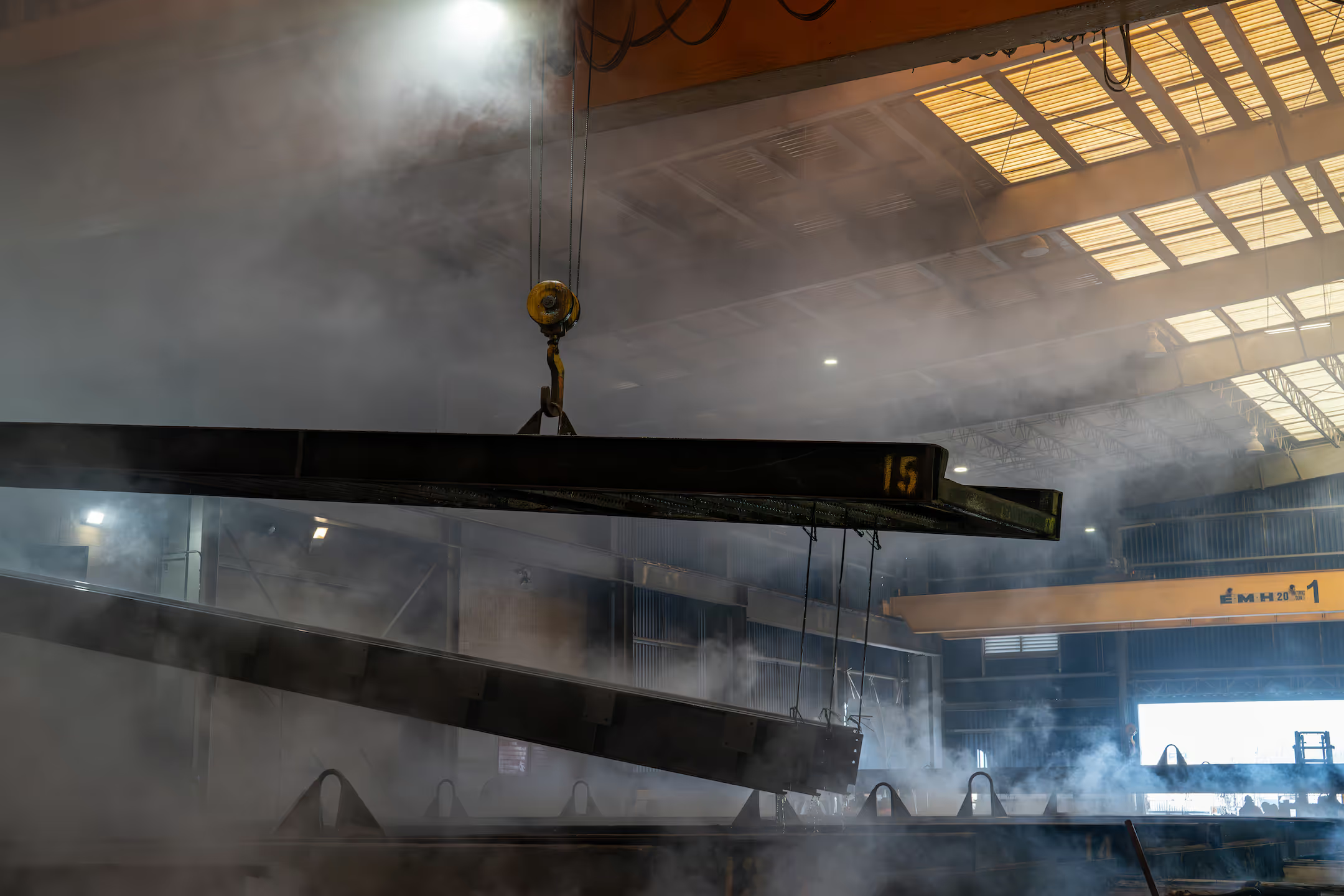