Industry-Leading Hot-Dip Galvanizing Process for Maximum Steel Protection
V&S Galvanizing's hot-dip galvanizing process delivers superior corrosion protection through advanced zinc coating technology. Our state-of-the-art facilities immerse fabricated steel in molten zinc at 840°F, creating metallurgically bonded zinc-iron alloy layers that provide unmatched durability and extended service life for structural steel components.
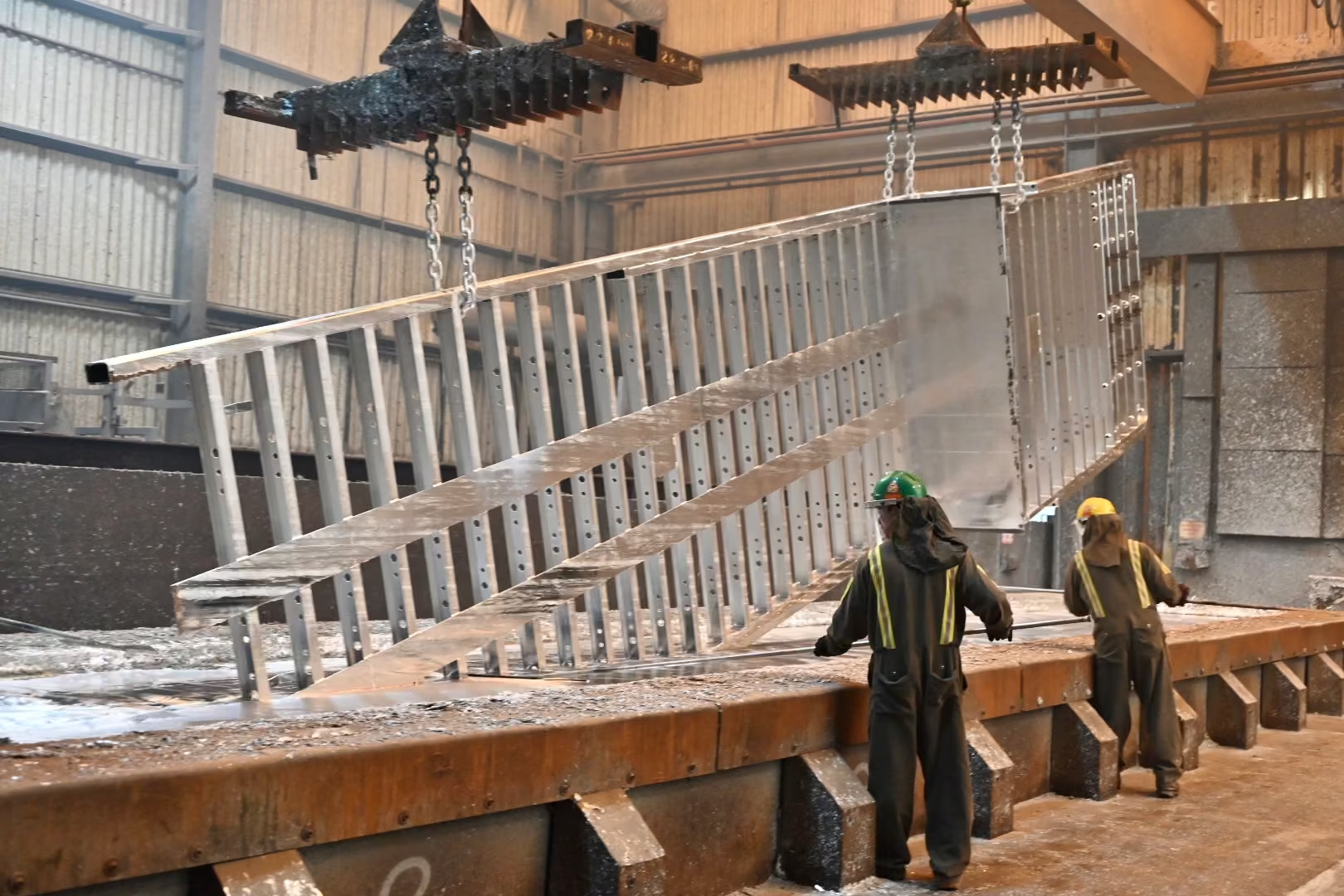
Our Proven 10-Step Hot-Dip Galvanizing Process Ensures Superior Results
Our comprehensive hot-dip galvanizing process follows strict ASTM standards to deliver consistent, high-quality zinc coatings. Each step is carefully controlled and monitored to ensure optimal coating thickness, adhesion, and corrosion protection performance that exceeds industry expectations.
Check In & Inspection
Comprehensive material evaluation and documentation to ensure steel components meet galvanizing requirements and identify any special handling needs.
Surface Preparation Assessment
Detailed analysis of steel surface conditions to determine optimal preparation methods and ensure proper zinc coating adhesion.
Caustic Cleaning
Advanced alkaline cleaning process removes oil, grease, organic residue, and water-based paint to prepare steel surfaces for galvanizing treatment. Please note that only organic residues and water-based paints will be removed in this step.
Rinse & Quality Check
Thorough water rinse removes cleaning residues and prepares steel for pickling treatment while maintaining quality control standards.
Pickling Trate
Hydrochloric acid treatment removes mill scale, rust, and oxidation to create clean steel surfaces essential for zinc bonding.
Secondary Rinse
Complete removal of pickling residues ensures optimal surface preparation and prevents contamination of subsequent process steps.
Flux Application
Zinc ammonium chloride flux coating prevents oxidation and promotes uniform zinc coating during the galvanizing immersion process.
Hot-Dip Galvanizing
Steel components are immersed in molten zinc at 840°F, creating metallurgically bonded zinc-iron alloy layers for maximum corrosion protection.
Quenching & Cooling
Controlled cooling process prevents thermal stress while maintaining coating integrity.
Final Inspection & Quality Control
Comprehensive testing including coating thickness measurement, adhesion testing, and visual inspection to ensure ASTM compliance and quality standards.
Check In & Inspection
Comprehensive material evaluation and documentation to ensure steel components meet galvanizing requirements and identify any special handling needs.
Surface Preparation Assessment
Detailed analysis of steel surface conditions to determine optimal preparation methods and ensure proper zinc coating adhesion.
Caustic Cleaning
Advanced alkaline cleaning process removes oil, grease, organic residue, and water-based paint to prepare steel surfaces for galvanizing treatment. Please note that only organic residues and water-based paints will be removed in this step.
Rinse & Quality Check
Thorough water rinse removes cleaning residues and prepares steel for pickling treatment while maintaining quality control standards.
Pickling Trate
Hydrochloric acid treatment removes mill scale, rust, and oxidation to create clean steel surfaces essential for zinc bonding.
Secondary Rinse
Complete removal of pickling residues ensures optimal surface preparation and prevents contamination of subsequent process steps.
Flux Application
Zinc ammonium chloride flux coating prevents oxidation and promotes uniform zinc coating during the galvanizing immersion process.
Hot-Dip Galvanizing
Steel components are immersed in molten zinc at 840°F, creating metallurgically bonded zinc-iron alloy layers for maximum corrosion protection.
Quenching & Cooling
Controlled cooling process prevents thermal stress while maintaining coating integrity.
Final Inspection & Quality Control
Comprehensive testing including coating thickness measurement, adhesion testing, and visual inspection to ensure ASTM compliance and quality standards.
Check In & Inspection
Comprehensive material evaluation and documentation to ensure steel components meet galvanizing requirements and identify any special handling needs.
Surface Preparation Assessment
Detailed analysis of steel surface conditions to determine optimal preparation methods and ensure proper zinc coating adhesion.
Caustic Cleaning
Advanced alkaline cleaning process removes oil, grease, organic residue, and water-based paint to prepare steel surfaces for galvanizing treatment. Please note that only organic residues and water-based paints will be removed in this step.
Rinse & Quality Check
Thorough water rinse removes cleaning residues and prepares steel for pickling treatment while maintaining quality control standards.
Pickling Trate
Hydrochloric acid treatment removes mill scale, rust, and oxidation to create clean steel surfaces essential for zinc bonding.
Secondary Rinse
Complete removal of pickling residues ensures optimal surface preparation and prevents contamination of subsequent process steps.
Flux Application
Zinc ammonium chloride flux coating prevents oxidation and promotes uniform zinc coating during the galvanizing immersion process.
Hot-Dip Galvanizing
Steel components are immersed in molten zinc at 840°F, creating metallurgically bonded zinc-iron alloy layers for maximum corrosion protection.
Quenching & Cooling
Controlled cooling process prevents thermal stress while maintaining coating integrity.
Final Inspection & Quality Control
Comprehensive testing including coating thickness measurement, adhesion testing, and visual inspection to ensure ASTM compliance and quality standards.
Advanced Galvanizing Capabilities Across 9 Locations
V&S Galvanizing operates one of North America's largest and most advanced hot-dip galvanizing networks, with nine state-of-the-art facilities strategically located to serve a wide range of industries and project scopes. Our multiple galvanizing kettles—including those capable of progressive dipping—accommodate everything from intricate components to oversized structural steel fabrications.
Each facility is equipped with modern material handling systems, overhead cranes, and custom fixtures to ensure safe and efficient processing of diverse steel products. Our kettle sizes range from small units for detailed parts to large tanks suitable for bridge girders and building frameworks, providing unmatched flexibility.
Why Choose V&S Galvanizing for Your Steel Protection Needs
Superior Corrosion Protection
Hot-dip galvanizing offers 50+ years of protection—even in coastal and industrial environments. Unlike paint, which sits on the surface, zinc bonds metallurgically at 3,600 psi, forming a durable alloy layer that protects even threaded and hard-to-reach areas.
Cost-Effective Lifecycle Value
Lowest Total Cost of Ownership Initial galvanizing investment pays for itself through eliminated maintenance costs, extended service life, and reduced replacement expenses over the structure's lifetime.
Complete Coverage Protection
360-Degree Steel Protection The immersion process ensures complete coating coverage including hard-to-reach areas, weld seams, and internal surfaces that other protection methods cannot adequately cover.
Fast Project Turnaround
With nine facilities and a flexible, customer-first approach, we ask: “How much steel, and when do you need it?” Our team works closely with you to meet tight construction and erection schedules—no generic turnaround promises, just reliable delivery when it matters most.
ASTM Compliance Guarantee
Certified Quality Standards All galvanizing work meets or exceeds ASTM A123 specifications with comprehensive documentation and testing to ensure compliance with engineering requirements.
Environmental Sustainability
Eco-Friendly Steel Protection Hot-dip galvanizing is 100% recyclable with minimal environmental impact, supporting green building initiatives and sustainable construction practices.
Hot Dip Galvanizing FAQ
Learn about our standard hot-dip galvanizing process, coating thickness specifications, size limitations, and corrosion protection standards.
Yes, but proper safety procedures are required due to zinc fumes. For extensive welding, we recommend galvanizing after welding completion. Masking is an option for areas that will need to be field welded post-galvanizing, and touch-up with zinc-rich paint can address any localized coating damage from welding.
Our approach is always "how much and when do you need it?" - turnaround time is typically 3-5 days depending on project size and facility scheduling. We offer expedited service when needed and work with your project timeline to ensure timely delivery.
Steel must be clean of any inorganic residues - our surface preparation process will handle organic residues. We provide comprehensive surface preparation including caustic cleaning, pickling, and flux treatment as part of our standard galvanizing process.
Hot-dip galvanizing adds thickness (typically 2-5 mils) which is generally accommodated in design tolerances. For threaded components, we recommend spin galvanizing to maintain thread integrity and dimensional accuracy.
Coating thickness varies based on steel thickness and composition, typically ranging from 2-5 mils (50-125 microns). We ensure all coatings meet or exceed ASTM A123 specifications with comprehensive thickness testing and documentation.
Our facilities can accommodate large steel components with varying kettle dimensions depending on the plant location. Please visit our plant location pages for specific kettle dimensions or call your sales rep for more details. We also offer progressive dipping for longer components that exceed single kettle dimensions.
Technical Resources for Hot-Dip Galvanizing Specifications
Access comprehensive technical documentation, design guidelines, and specification resources to optimize your hot-dip galvanizing projects. Our expert team provides detailed engineering support and educational materials to ensure successful project outcomes and long-term performance.
Calculator
Estimate project turnaround and zinc usage with this galvanizing calculator. Plan smarter with quick, accurate insights tailored to your specifications.
Docs
Download detailed technical specifications, material guidelines, and coating standards to support your engineering and fabrication needs.
News
Stay informed with industry updates, company news, and best practices for corrosion protection and steel performance.
FAQs
Get answers to common questions about our galvanizing services, coating performance, project prep, and more—straight from the experts.