One Times Square

The Challenge, The Solution, The Results
Working around the existing 1906 structure, One Times Square presented interesting design and field challenges for Orange County Iron Works and Gabriel Steel Erectors. To save time, hot dip galvanizing was used in the interior of the building for all the HHS splice connections and typical beams instead of a primer paint system.
The outer skeleton façade is made up of all galvanized steel tubing and beams to provide decades of maintenance-free corrosion protection. The specifier chose to utilize galvanized steel for just that reason; to avoid the costly routine repair of a paint system, the idea was to install the hot dip galvanized steel and not have to give thought to maintenance: a ‘set it and forget it approach’.
The 220 tons tube and beam for the skeleton came in truckloads of steel that were turned around in two days by the galvanizer. No other coating system could have been applied as quickly as hot dip galvanizing. The quick turnaround of the factory-controlled hot dip galvanizing process allowed the galvanizer to match the different components together and ship directly to the job site.
“The building’s next chapter will build on that legacy, creating a new destination in the heart of Times Square for the next generation.”
The 120-year-old One Times Square, formerly the headquarters for The New York Times, is undergoing renovations for a new museum experience and viewing deck that will provide visitors with an elevated perspective of Times Square and a view of the one and only New Year's Eve Ball--and AISC and the Structural Engineers Association of New York recently hosted a site visit to take a closer look!
Check out a few highlights of the site tour, including a view of that famously festive ball and a peek at some of the architecturally exposed structural steel (AESS) elements on the new deck.
Protecting America's Infrastructure One Dip at a Time
.avif)
Tait Ave Bridge
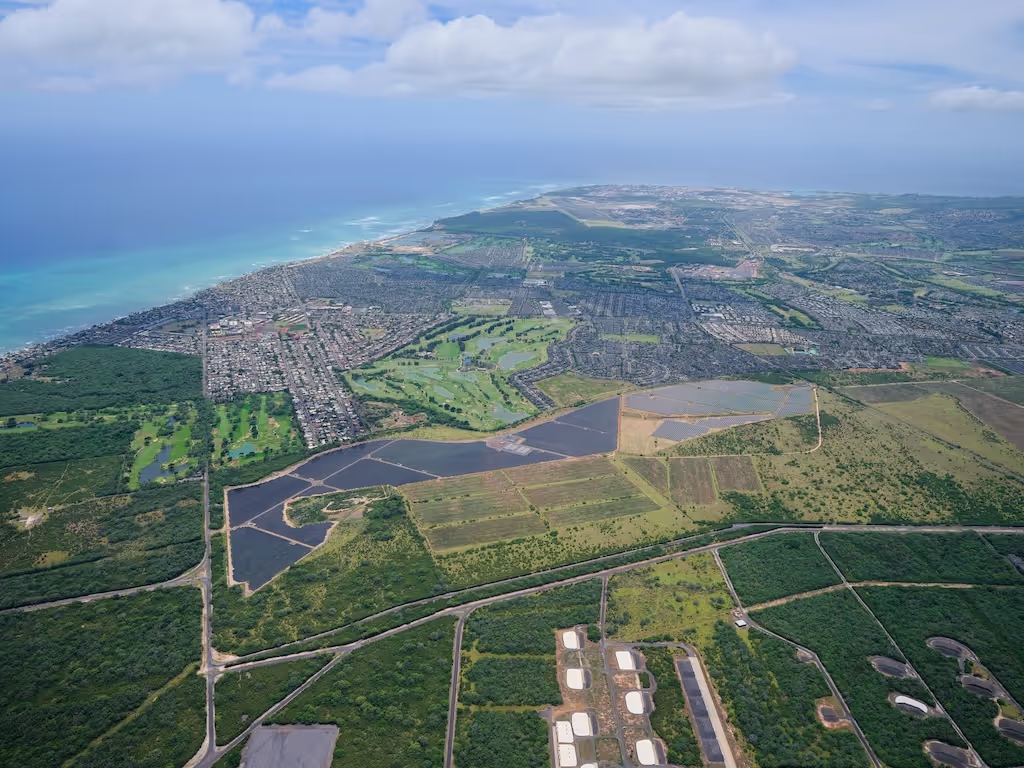
APA Hawaii Solar
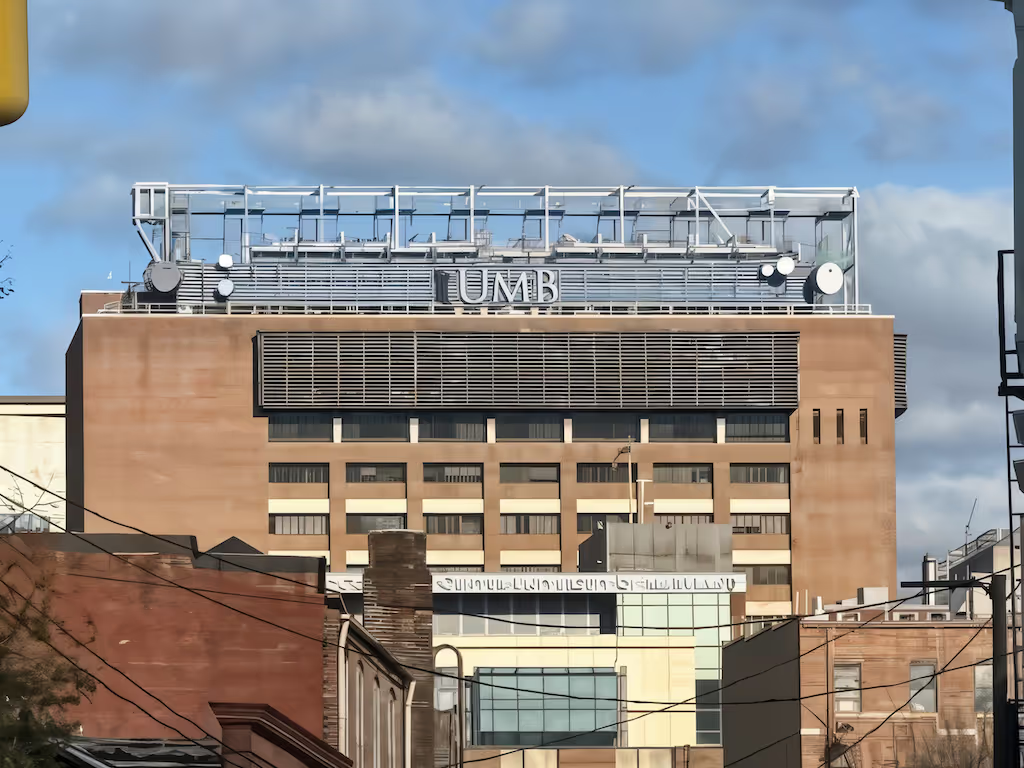
UMB Maintenance Bay
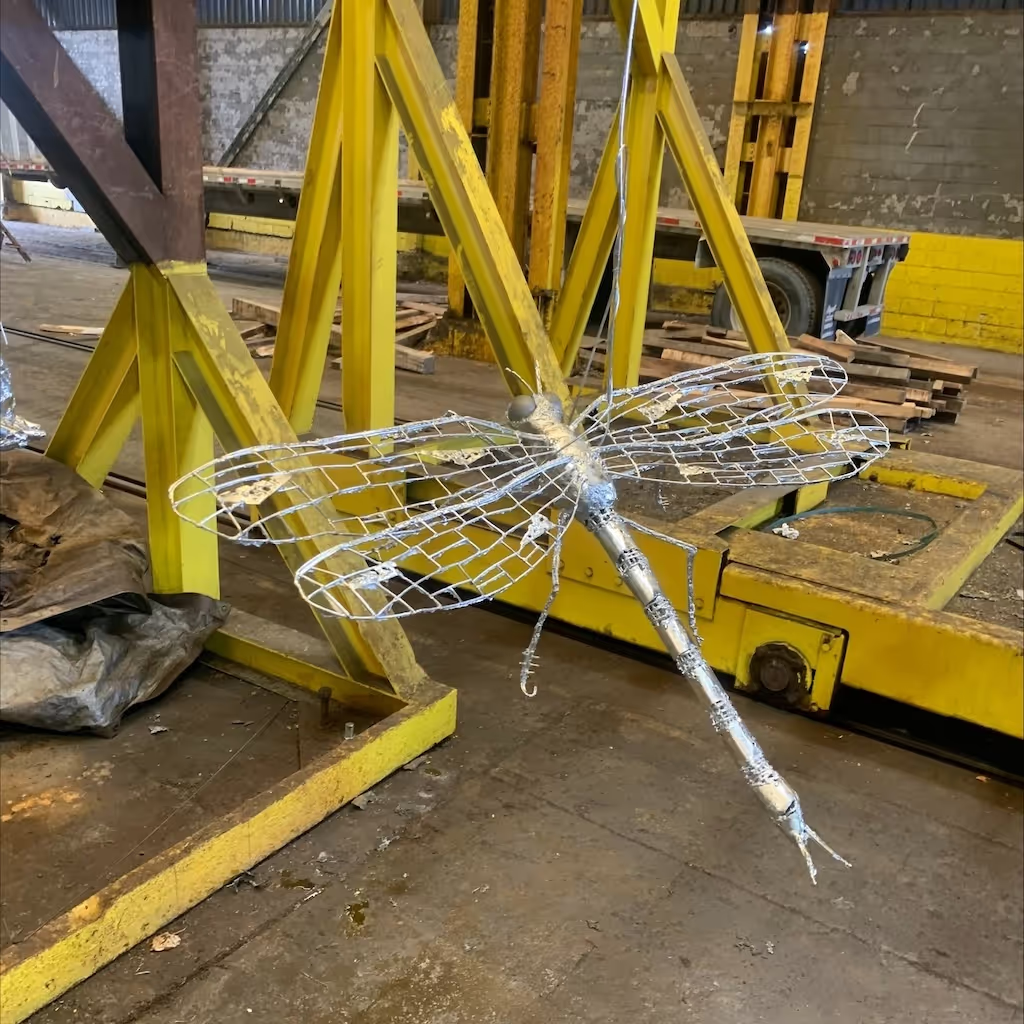
William Allen Art
Ready to Transform Your Project with Industry-Leading Galvanizing?
Don't let corrosion compromise your investment. Partner with V&S Galvanizing for proven protection that outlasts the competition. Our expert team delivers custom solutions, rapid turnaround, and nationwide reliability that keeps your project on schedule and on budget.
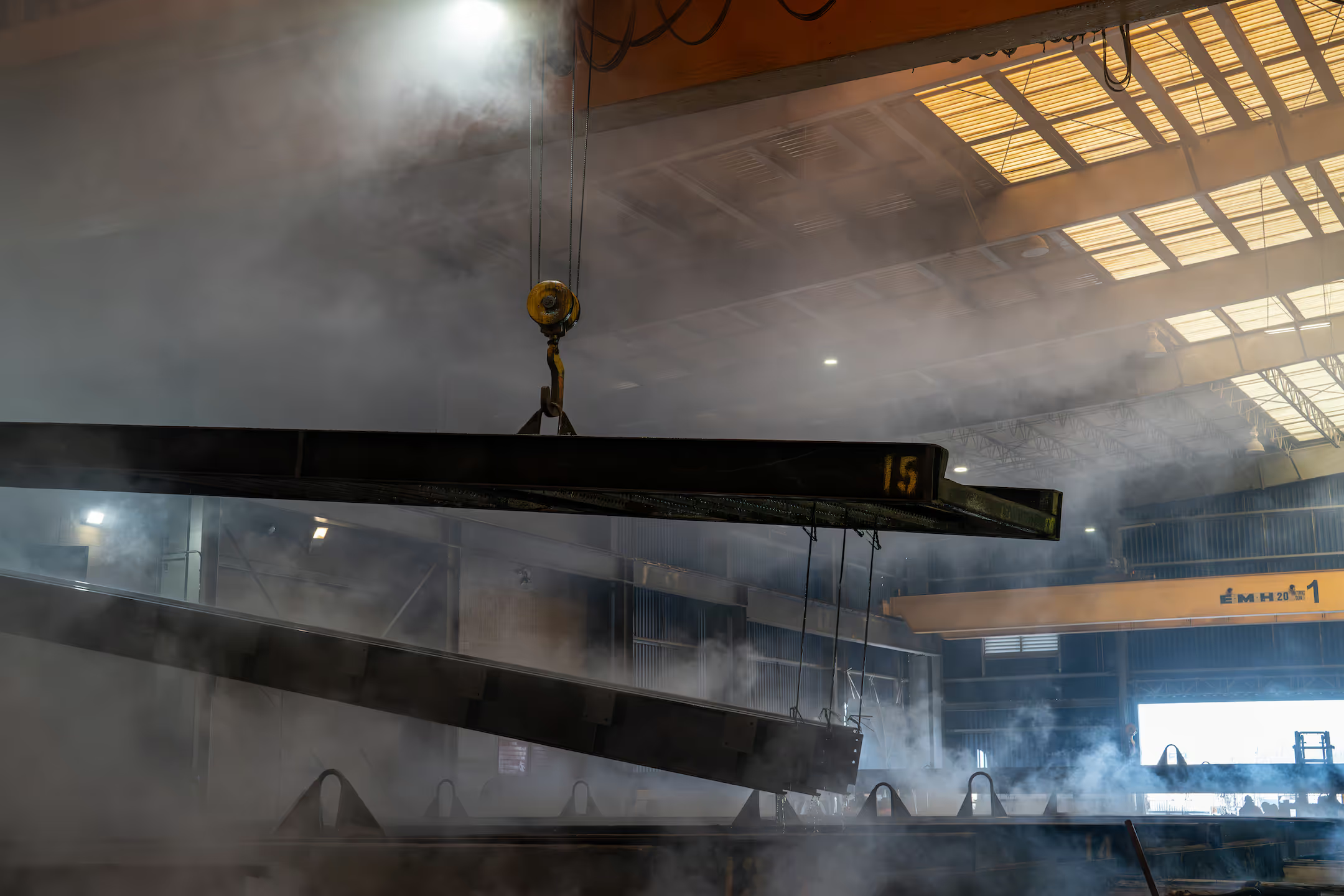