Pinecrest I74 Bridge

The Challenge, The Solution, The Results
The replacement structure consists of a two-span bridge that measures 214 feet from back-to-back of abutments, with an out-to-out width of 75 feet – 10 inches. The bridge carries two, 14-foot traffic lanes, 8-foot outside shoulders, a 12-foot left-turn lane, and a 10-foot-wide multi-use path on the east side of the structure. The structure was constructed utilizing stage construction to maintain one lane of traffic in each direction.
The superstructure consists of a cast-in-place concrete deck supported by hot dip galvanized composite plate girders. The decision to Hot Dip Galvanize the steel in this bridge comes from the value of longevity that galvanizing provides.
“IDOT has realized the value hot dip galvanized steel can offer in the longevity of their bridge projects and we continue to see galvanizing specified more often.”
Protecting America's Infrastructure One Dip at a Time
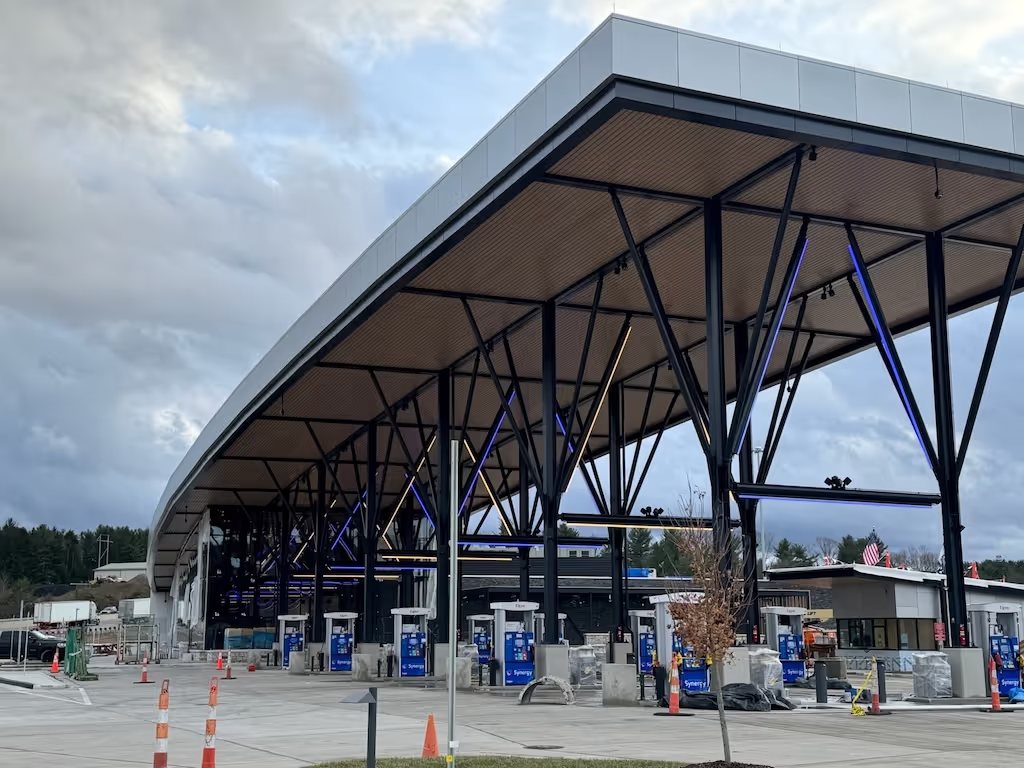
Bluestone Travel Plaza
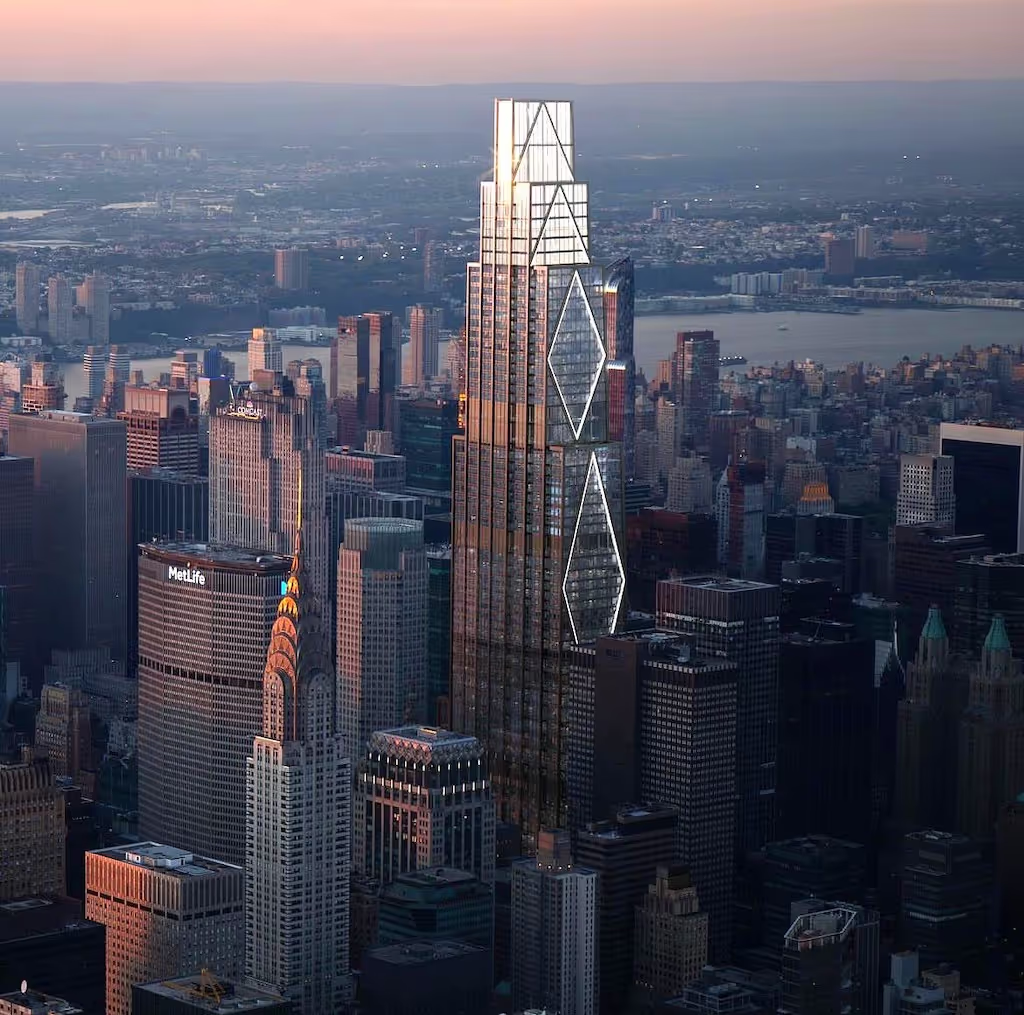
JPMorgan Chase 270 Park Ave
.avif)
Bridge Port I
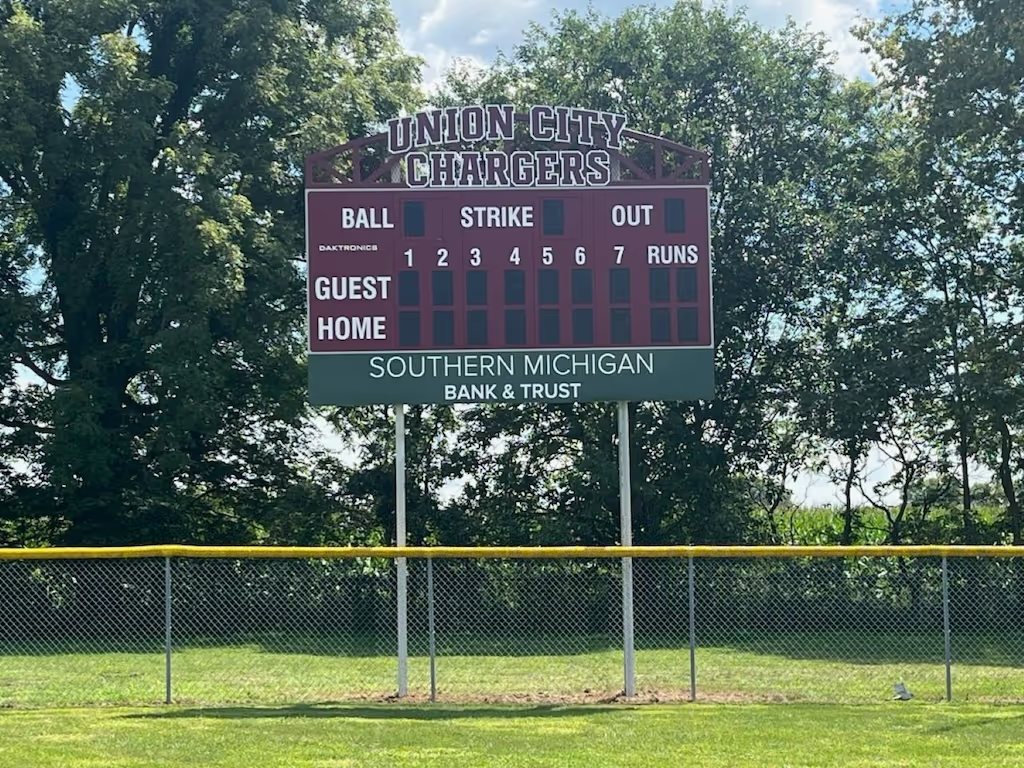
Union City Scoreboard
Ready to Transform Your Project with Industry-Leading Galvanizing?
Don't let corrosion compromise your investment. Partner with V&S Galvanizing for proven protection that outlasts the competition. Our expert team delivers custom solutions, rapid turnaround, and nationwide reliability that keeps your project on schedule and on budget.
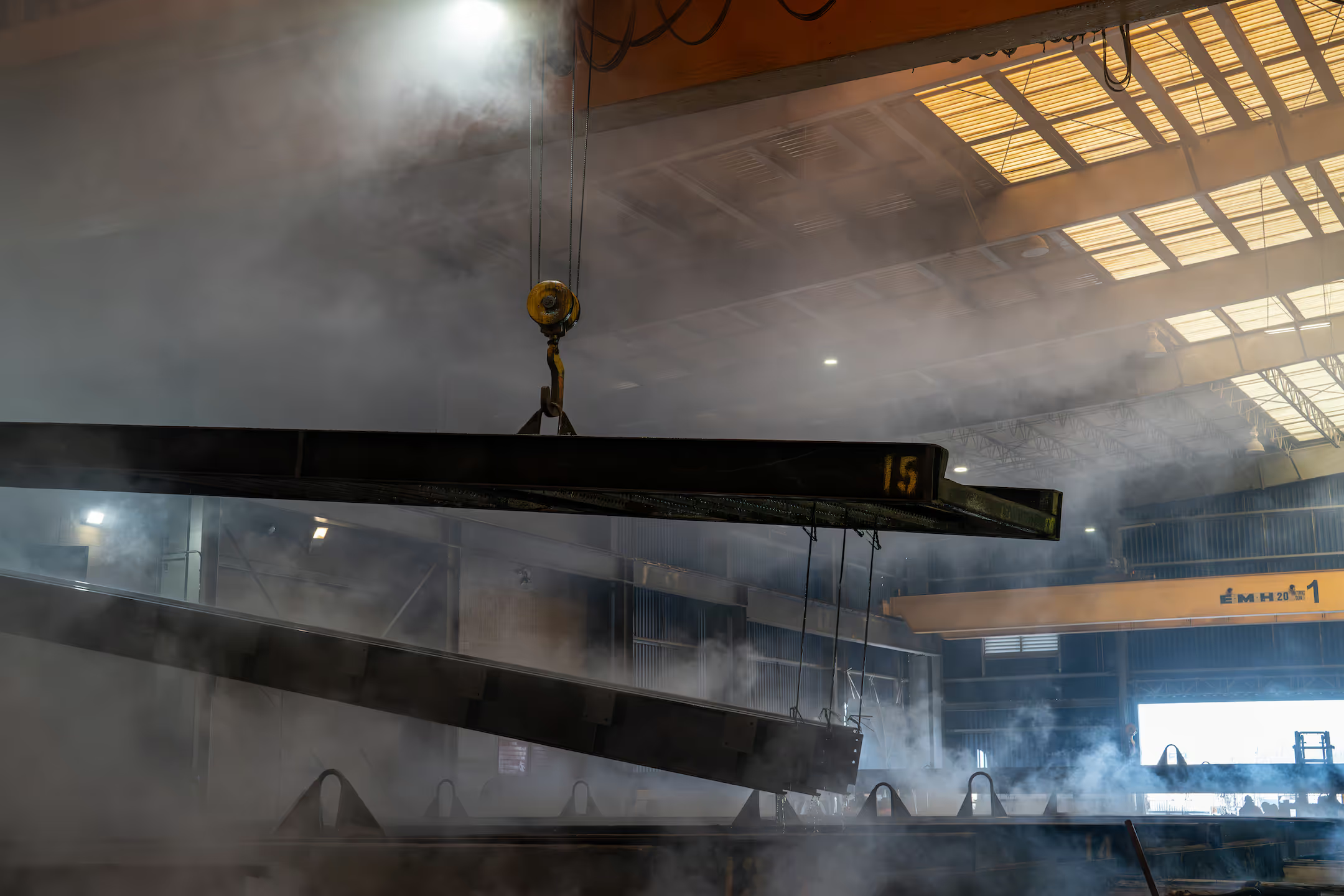