Stonebridge Great Lakes
.avif)
The Challenge, The Solution, The Results
Great Lakes Cheese Co. has put a lot of thought into the location and construction of their newest cheese production plant. In place of an operating plant in nearby Cuba, NY- the location is close enough that most employees will continue with the company. With job growth from the current 200 employees to approximately 400, the plant will draw employees from many nearby towns. Construction wrapped in 2024 on the massive, 486,000-square-foot, $621 million Great Lakes Cheese Co. plant along Route 16 in Franklinville, NY. Some production equipment was so big it had to be placed inside the walls using a crane before the roof was completed. Area dairy farmers and co-ops are gearing up to provide the new plant with up to 4 million gallons of milk a day, twice what the Cuba plant currently uses. The plant will produce American and Italian-style cheeses including cheddar and natural American cheese for much of the East Coast.
The galvanizer worked closely with Stone Bridge Iron and Steel to galvanize 1400 tons of large structural and tubular steel for the Great Lakes Cheese project in Franklinville, NY. Through quick turnarounds and pre-loaded trailers for an easy drop and pick for the truck drivers, the galvanizer was able to meet the tight schedule demanded of this project. Due to the anticipation of division of the construction labor force that would come from other large projects in the region, Great Lakes Cheese had a tight schedule to meet in order to utilize labor while it was available. Due to size of the material used in this project, many members had to be progressively dipped by the galvanizer. Box beams, Tubes and Girts were among the various shapes that went into this large structure. The galvanizer provided additional services by plugging the vent and drain holes on the tubular material, with some plugs exceeding 3 inches in diameter due to the size of the tubes. Some of the cheese production equipment is so large, it had to be installed by crane prior to the addition of roofing to the building. The use of Hot Dip Galvanized steel will ensure that the steel used to build this plant will remain protected from corrosion for many years to come.
Protecting America's Infrastructure One Dip at a Time
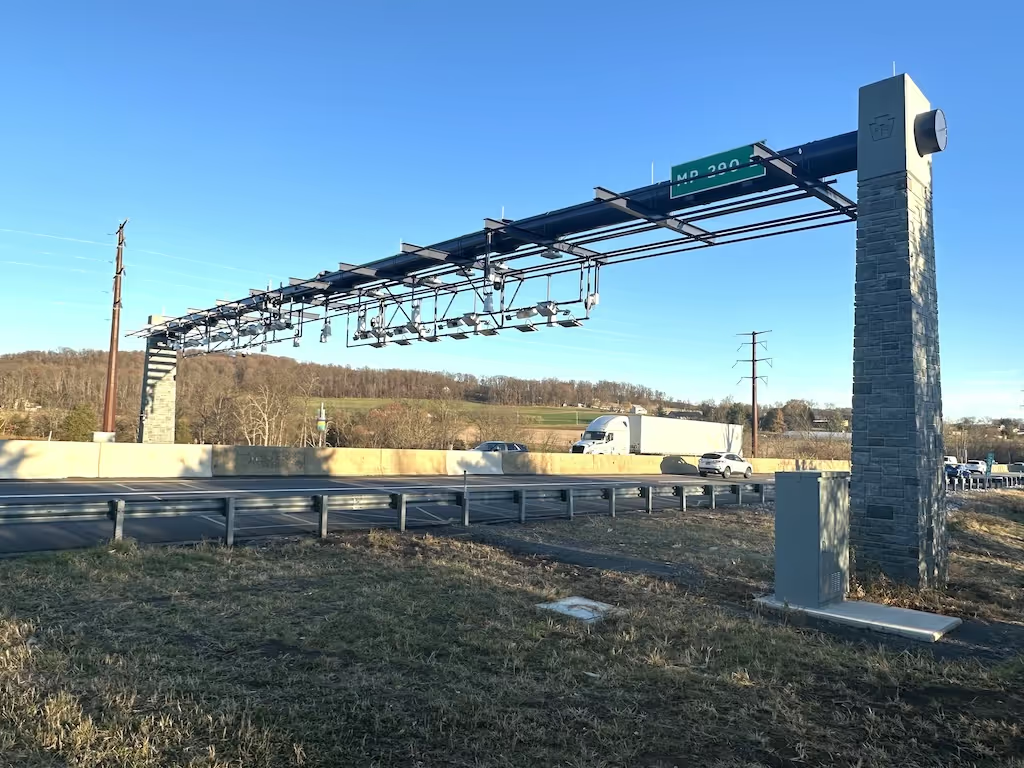
Pennsylvania Turnpike Road Tolling
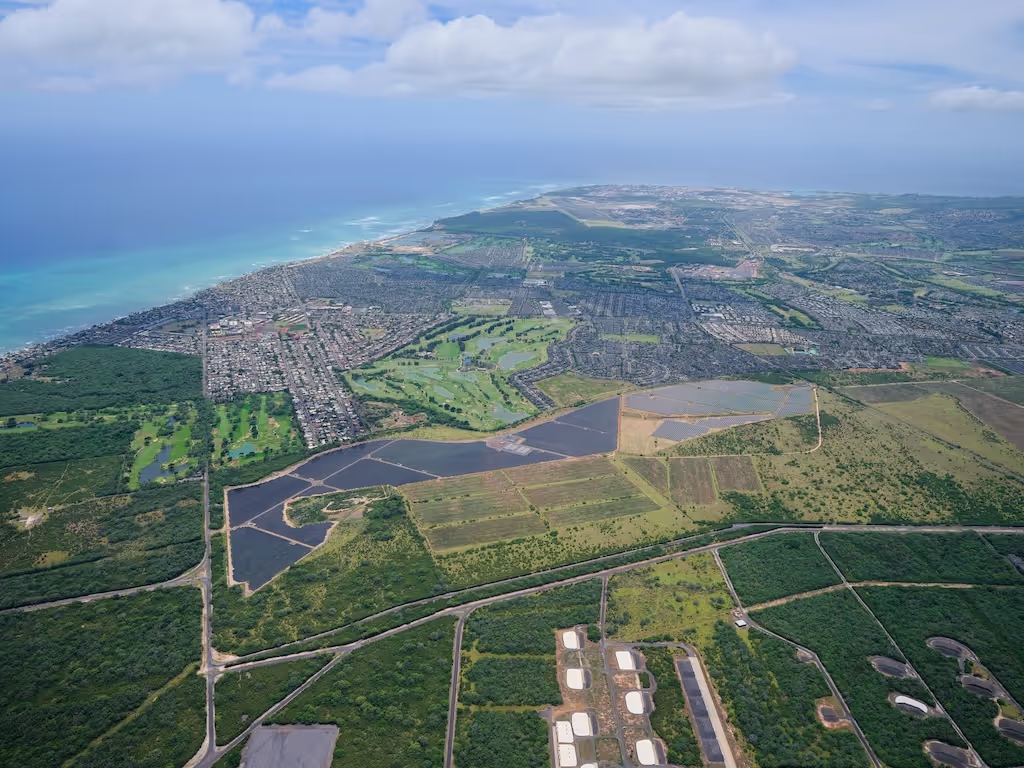
APA Hawaii Solar
.avif)
Stonebridge Great Lakes
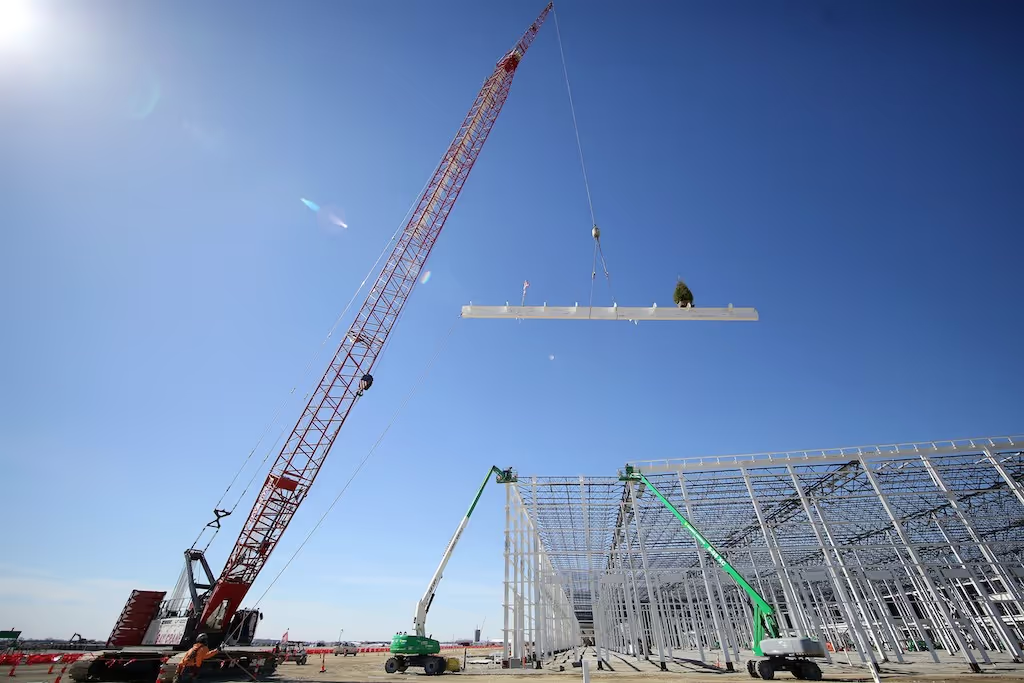
EV Battery Plant
Ready to Transform Your Project with Industry-Leading Galvanizing?
Don't let corrosion compromise your investment. Partner with V&S Galvanizing for proven protection that outlasts the competition. Our expert team delivers custom solutions, rapid turnaround, and nationwide reliability that keeps your project on schedule and on budget.
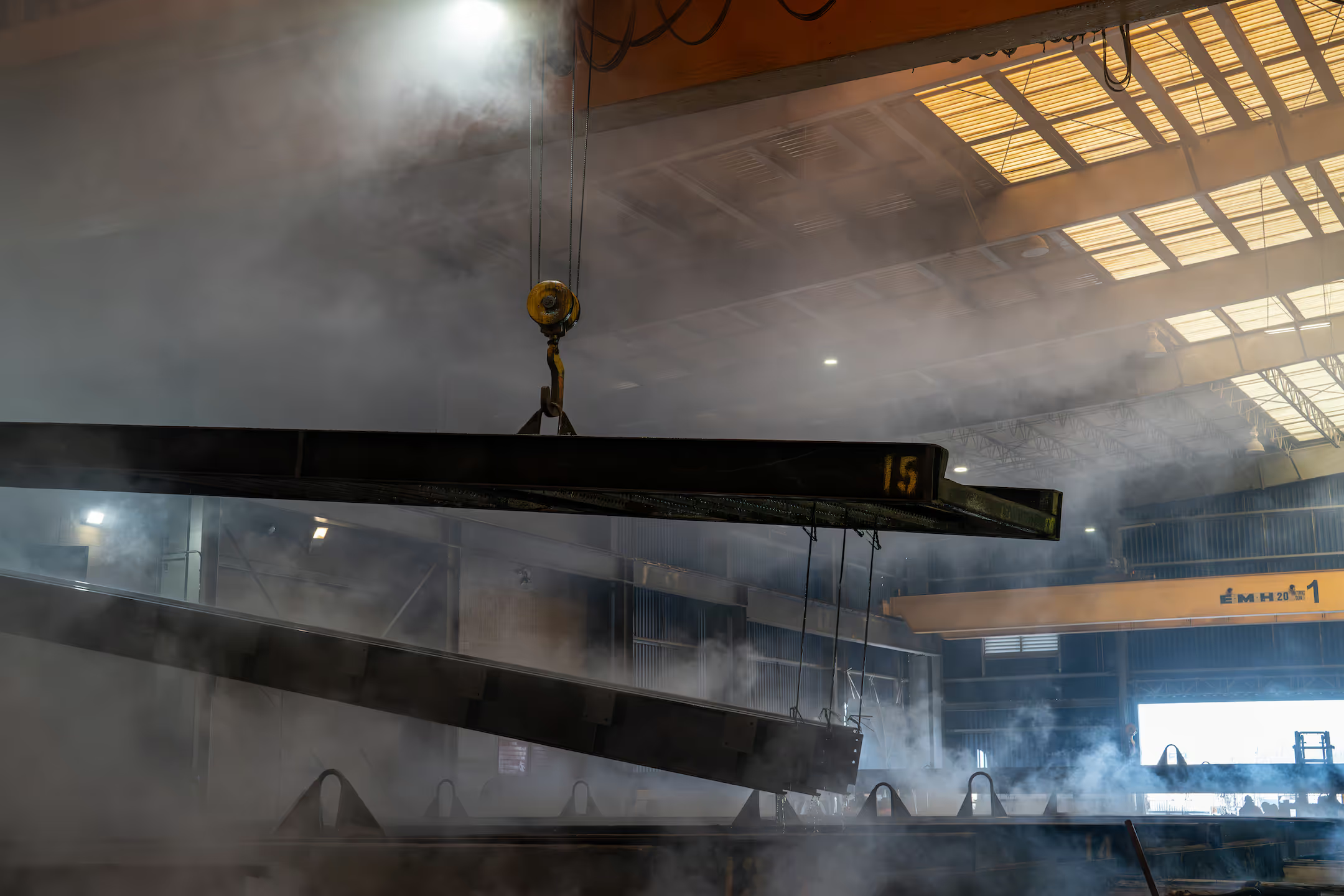