St. George’s Bridge

The Challenge, The Solution, The Results
In April 2023, the St. George’s Bridge closed for an 18-month renovation, including work to the concrete deck, steel barrier, scuppers, drainage pipes, finger joints, and bridge railing. The purpose of the repairs is to improve the structural condition and the travel surface of the bridge. The Hot Dip Galvanized coating will allow these repairs to survive the east coast elements for decades to come.
The prior bridge rail and barriers were not hot-dip galvanized decades ago and were showing signs of corrosion. Due to the longevity of the galvanized coating, HDG was an easy decision for the Army Corps of Engineers. The bridge rail, which matches the light gray color of the bridge beam and local refinery plants across the canal, did not receive any paint or powder coating, as it is an aesthetic match. Although the C&D Canal is in the Mid-Atlantic region, which gets the worst of summer and winter climates, the longevity of HDG will help this bridge last many more decades.
The C&D Canal connects the Chesapeake Bay and the Delaware River. One of its oldest bridges, the St. George’s Bridge built in 1941, accommodates 11,000 vehicles per day. After another major highway opened decades ago, the St. George’s Bridge is no longer the well-traveled bridge it once was, but it was still in need of repair on the decking and rail.
During a ribbon cutting ceremony, Philadelphia District Commander Lt. Col. Jeffrey Beeman stated the importance of quality, time, and budget. He said, “We have a saying in the Army Corps of Engineers, we safely deliver projects on time and within budget – we don't always hit all four of those. We prioritize safety and quality because that's what everybody remembers. But we really nailed all four on this project”. Time was an important aspect of this project, as one local business owner stated that the bridge closure had cost him thousands of dollars of revenue during the renovation. With just four bridges spanning over the C&D Canal, between two states, it was essential to stay within the project timeline. Between the decking and steel components that were arriving to the jobsite, the efficiency of hot-dip galvanizing made it possible to stay within the specified timeline.
Speaking to the longevity of the bridge and its future, State Senator Nicole Poore said:
“It is now codified in legislation that this bridge will not be torn down, but instead will always be maintained for future generations.”
Protecting America's Infrastructure One Dip at a Time

Knoebels Giant Log Flume
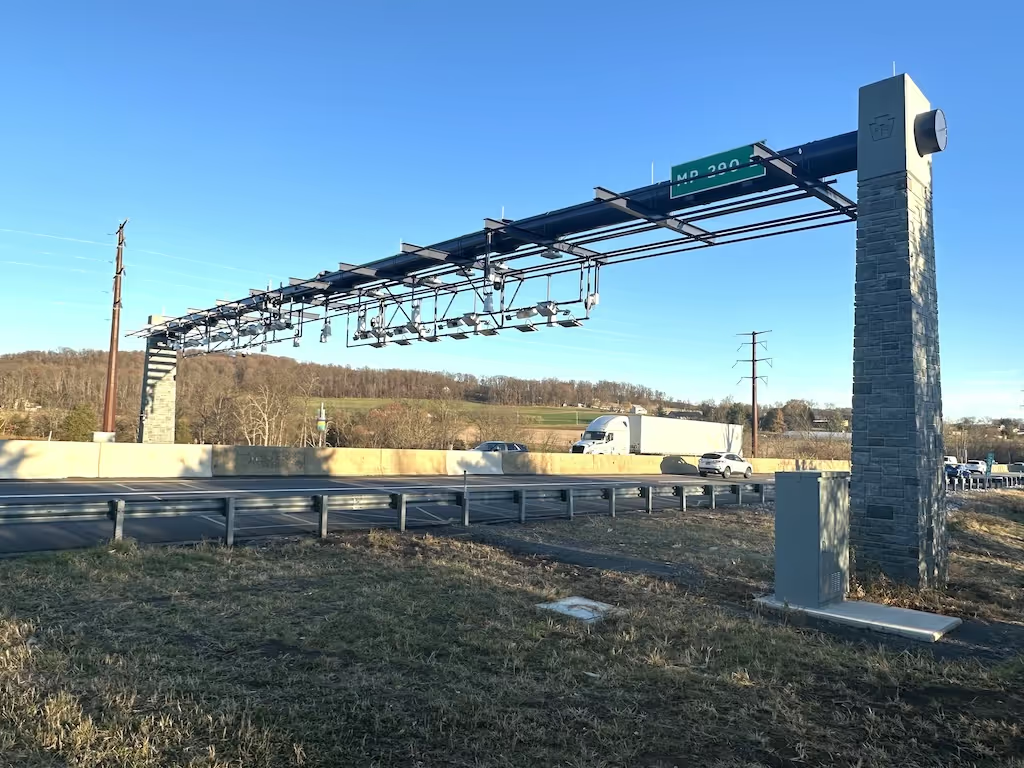
Pennsylvania Turnpike Road Tolling
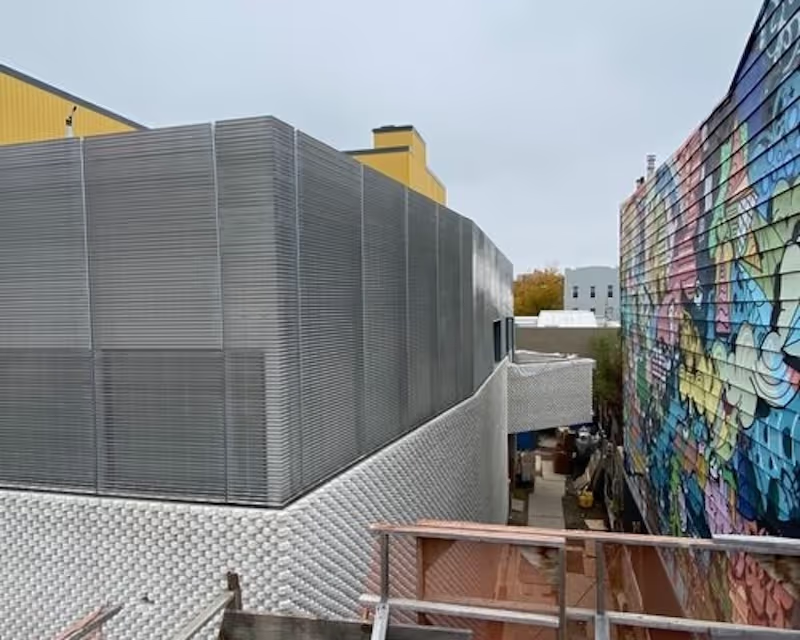
Maujer Street Facade
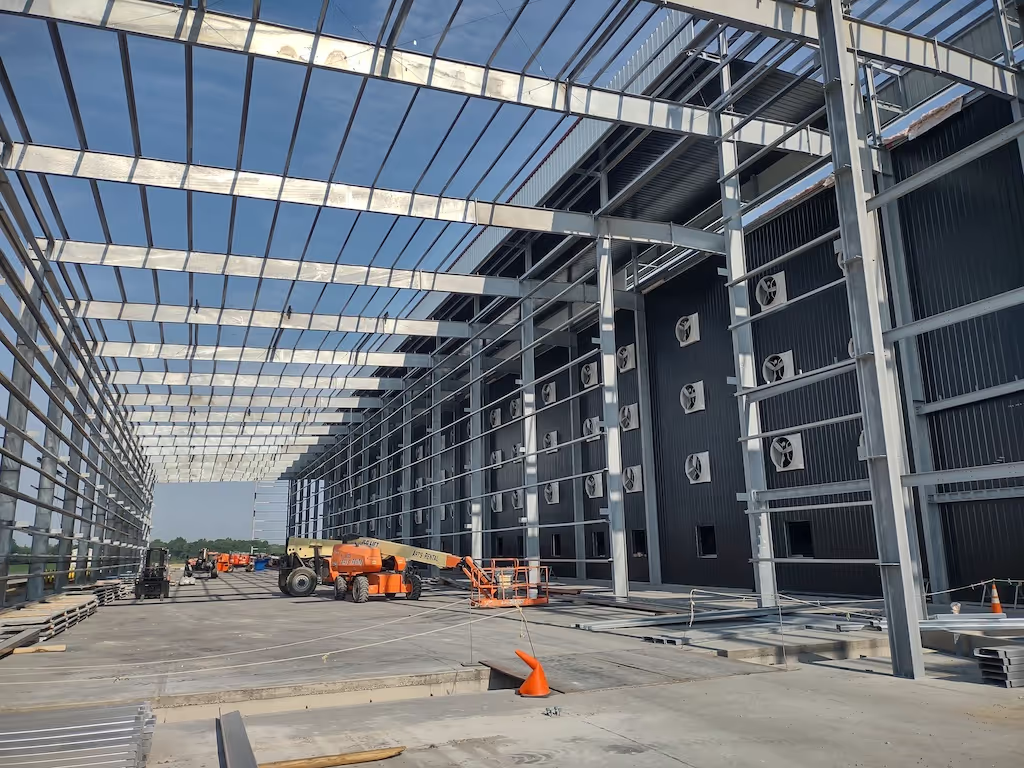
Golden Giant Egg Processing Facility
Ready to Transform Your Project with Industry-Leading Galvanizing?
Don't let corrosion compromise your investment. Partner with V&S Galvanizing for proven protection that outlasts the competition. Our expert team delivers custom solutions, rapid turnaround, and nationwide reliability that keeps your project on schedule and on budget.
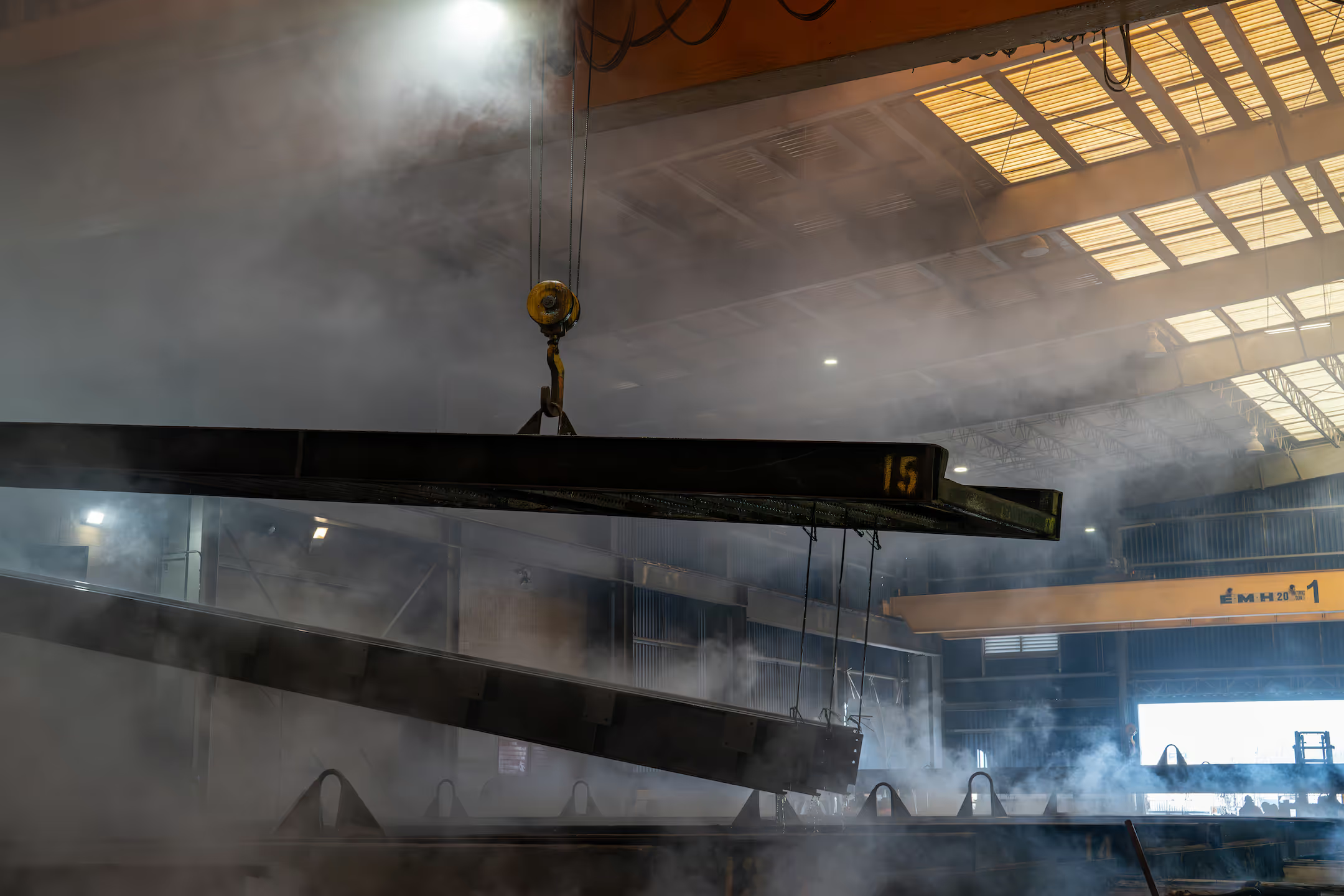