Understanding HDG Revisions in the AASHTO LRFD Bridge Design Specifications, 10th Edition
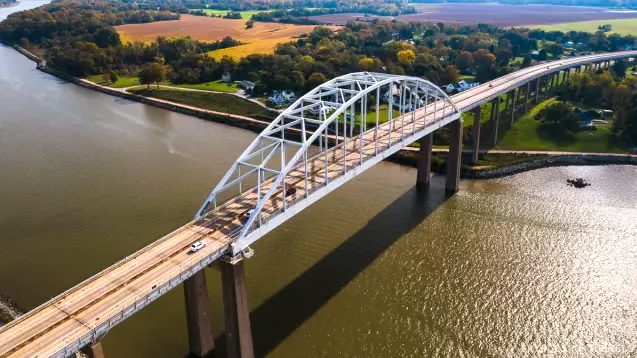
Introduction to Hot-Dip Galvanizing in Bridge Design
Hot-dip galvanizing (HDG) is a trusted corrosion protection method for steel bridge components, offering durability, cost-effectiveness, and sustainability. The American Association of State Highway and Transportation Officials (AASHTO) Load and Resistance Factor Design (LRFD) Bridge Design Specifications, 10th Edition, released in 2024, includes significant revisions to Section 6 (Steel Structures) that impact HDG applications. These updates, approved by the AASHTO Steel & Metals Committee, enhance the design and specification of galvanized steel for bridge projects, ensuring compliance with federal standards for infrastructure durability. At V&S Galvanizing, we provide engineers and architects with expert HDG solutions tailored to these updated specifications, supporting safe and long-lasting bridge infrastructure across North America.
Key Revisions Affecting HDG in AASHTO LRFD 10th Edition
The 10th Edition introduces critical updates to Article 6.13.2.8, focusing on slip-critical connections involving HDG faying surfaces. Below, we break down the key changes and their implications for bridge design:
1. Creep Reduction Factor for HDG Faying Surfaces
A new creep reduction factor, Kc = 0.80, has been introduced to the equation for calculating the nominal slip resistance (Rn) of galvanized faying surfaces classified as Class C (slip coefficient µ = 0.30). This factor accounts for long-term creep behavior in galvanized connections, ensuring accurate design for load-bearing bolted joints. For duplex-coated systems (coatings applied over HDG), a higher slip coefficient of Class D (µ = 0.45) is specified, offering enhanced slip resistance for specific applications. These updates provide engineers with precise parameters to optimize connection designs while maintaining safety and durability.
2. HDG and Metallizing for Mixed Steel Components
Bridge projects often combine large steel fabrications (e.g., plate girders too large for HDG) with smaller, complex components (e.g., cross frames, railings, cable stay tubes) suitable for galvanizing. The 10th Edition now classifies connections between a hot-dip galvanized faying surface and a metallized faying surface as Class D (µ = 0.45). This eliminates the need for time-consuming slip testing, which previously took months and was subject to limited laboratory availability. By standardizing this classification, the specification simplifies design and reduces costs while leveraging the corrosion resistance of both HDG and metallizing. Successful implementations include projects like the I-95 Overpass at Fairfield Avenue (CT), Kosciuszko Bridge (NY), and I-90 Overpass at Commonwealth Ave. (MA).
3. Elimination of Wire Brushing for HDG Faying Surfaces
Previous practices required wire brushing of HDG faying surfaces to enhance slip properties, adding labor and costs. Industry research, reflected in both the AASHTO LRFD (8th Edition, 2017) and the Research Council on Structural Connections (RCSC) Specification (2020), determined that wire brushing does not improve slip performance and is now prohibited. This change, carried forward in the 10th Edition, streamlines the galvanizing process, saving time and reducing expenses for galvanizers, fabricators, and specifiers.
Benefits of HDG for Bridge Projects
Hot-dip galvanizing remains a preferred choice for bridge infrastructure due to its proven advantages, which align with the AASHTO LRFD updates:
- Superior Corrosion Protection: HDG creates a metallurgically bonded zinc-iron alloy coating that protects steel from harsh environmental conditions, extending service life in moisture-heavy bridge environments.
- Cost Efficiency: By eliminating maintenance needs and reducing labor (e.g., no wire brushing), HDG lowers lifecycle costs, as demonstrated in projects like the Kosciuszko Bridge.
- Sustainability: Galvanized steel is 100% recyclable, supporting environmentally responsible bridge construction.
- Design Flexibility: The updated Class D classification for HDG-metallized connections expands coating options, enabling innovative designs for mixed steel components.
Why Engineers and Architects Choose V&S Galvanizing
V&S Galvanizing is a leader in delivering HDG solutions compliant with the latest AASHTO LRFD specifications. Our expertise ensures that your bridge project benefits from:
- Compliance with Standards: We adhere to ASTM A123 and A153, as well as AASHTO LRFD requirements, ensuring quality and reliability.
- Advanced Facilities: Our state-of-the-art galvanizing plants process steel components of varying sizes, from railings to structural supports, with precision.
- Technical Support: Our team collaborates with engineers and architects to provide design guidance, coating specifications, and project-specific solutions.
- Proven Track Record: We’ve supported major bridge projects across North America, delivering durable, maintenance-free components.
Practical Applications of HDG in Bridge Design
The AASHTO revisions enhance HDG’s applicability for various bridge components, including:
- Slip-Critical Connections: Bolted joints in girders and cross frames benefit from updated slip coefficients, ensuring structural integrity.
- Railings and Cross Frames: Smaller components gain long-term corrosion protection, reducing maintenance costs.
- Cable Stay Tubes: HDG-metallizing combinations provide durability for complex, high-visibility elements.
How to Specify HDG for Your Bridge Project
To incorporate HDG into your bridge design per the AASHTO LRFD 10th Edition:
- Review Specifications: Consult Article 6.13.2.8 for slip-critical connection requirements, including creep reduction factors and surface classifications.
- Select Coating Systems: Choose Class C (HDG only) or Class D (HDG with metallizing or duplex coatings) based on project needs.
- Partner with V&S Galvanizing: Contact our technical team for guidance on coating thickness, surface preparation, and compliance.
- Verify Quality: Ensure galvanizing meets ASTM standards through rigorous inspections, as provided by V&S Galvanizing.
Additional Resources
For further information, explore these resources:
- AASHTO LRFD Bridge Design Specifications, 10th Edition
- American Galvanizers Association: Slip Resistance of HDG Faying Surfaces
- V&S Galvanizing Technical Support
Contact V&S Galvanizing Today
Ready to leverage hot-dip galvanizing for your bridge project? V&S Galvanizing offers industry-leading expertise to meet AASHTO LRFD standards and deliver durable, sustainable steel components. Contact us to discuss your project or request a quote.
Call: (614) 443-4621
Email: columbus@hotdipgalvanizing.com
Website: https://hotdipgalvanizing.com
Conclusion
The AASHTO LRFD Bridge Design Specifications, 10th Edition, streamlines the use of hot-dip galvanizing in bridge projects, offering engineers and architects clear guidelines for slip-critical connections and mixed coating systems. By partnering with V&S Galvanizing, you gain access to cost-effective, sustainable, and compliant HDG solutions that enhance the durability of steel infrastructure. Stay ahead of industry standards and build bridges that last with V&S Galvanizing.
Let’s get your project on the schedule—tell us what you need and when you need it.
Put This Galvanizing Knowledge to Work on Your Next Project
Every day you delay galvanizing decisions costs you money in future maintenance and replacements. V&S Galvanizing's technical experts are ready to review your specifications, answer your questions, and deliver the corrosion protection solution that saves you time and budget long-term.
Explore More Galvanizing Innovations & Insights
Discover the latest advancements, projects, and sustainability initiatives in the hot-dip galvanizing industry with V&S Galvanizing.